I mattoni e le statuine in porcellana della nonna, in fondo, hanno qualcosa in comune: una storia millenaria e affascinante, un processo produttivo complesso, e le stesse materie prime, o quasi. Stiamo per vedere come si produce la ceramica, il minimo comune denominatore di mattoni, statuine e… piastrelle.
La produzione della ceramica è molto antica. Ben presto l’uomo si è accorto che l’argilla bagnata è malleabile e può essere lavorata facilmente con le mani, mentre quando è asciutta diventa rigida. Quando invece viene cotta ad alta temperatura subisce una trasformazione irreversibile, e diventa solida e compatta in modo permanente. I primi manufatti in argilla risalgono al periodo neolitico, quando vasi, piatti e bicchieri venivano cotti direttamente sul fuoco.
In questo articolo cercheremo di capire meglio cos’è la ceramica, come viene lavorata e decorata. Ovviamente, anche in questo caso c’entra la stampa a getto d’inchiostro. Per circoscrivere un pochino l’argomento, ci occuperemo soprattutto di piastrelle, ovvero di produzione e decorazione di oggetti piani. Di stoviglie, ceramica funzionale e sanitaria parleremo un’altra volta. Questo settore è molto specialistico, è difficile entrarci senza competenze elevate e investimenti importanti (alla fine dell’articolo avrai capito il perché). Per questo, se lavori nelle arti grafiche, difficilmente ti occuperai di decorazione industriale ceramica. Se hai una stampante flatbed magari ti capiterà di stampare piastrelle decorative, ma difficilmente questo sarà il tuo business principale. Eppure ti invito a continuare a leggere, per due motivi: il primo è che l’Italia è tra i maggiori produttori di ceramica al mondo, leader nei prodotti di alta gamma, nell’estetica di superficie, nel valore delle quantità esportate e nelle tecnologie; il secondo è che in questo settore l’inkjet è penetrata in modo rapidissimo e capillare. In meno di dieci anni dalla comparsa di questa tecnologia nel settore si è arrivati a una diffusione di oltre il 95% nei mercati “maturi” come Italia o Spagna.
Come sempre, ci sono alcune domande-guida che hanno fatto e fanno da filo conduttore in questo articolo:
- Qual è la destinazione d’uso del prodotto finito?
- Dove verrà usato il prodotto finito?
- Che resistenze sono necessarie?
- Quali lavorazioni sono necessarie per arrivare al prodotto finito?
- Quali tecniche di decorazione posso usare?
La lavorazione di piastrelle ceramiche oggi è principalmente industriale. Le aziende produttrici si chiamano “ceramiche”; le loro linee di produzione sono estremamente produttive e richiedono competenze tecniche specifiche, spesso custodite gelosamente. Non parleremo di stampa organica (tipo UV o UV LED) ma di stampa ceramica. Seguiremo una linea di produzione industriale, che usa inchiostri inorganici che hanno bisogno di una cottura.
Pasta porosa – Colorata
- Terrecotte (maiolica) – Non rivestite
- Faenze – Rivestite
- Laterizi – Non rivestiti
- Gres sanitari – Rivestiti
Pasta porosa – Bianca
- Terraglie forti
- Terraglie deboli
Pasta compatta – Colorata
- Gres – Rivestiti
- Gres – Non rivestiti
Pasta compatta – Bianca
- Porcellane – Rivestite
- Porcellane (biscuit) – Non rivestite
La composizione del corpo ceramico
Le materie prime che servono a produrre le piastrelle di ceramica sono di origine minerale. Vengono usati principalmente silicati: argille, le cui proprietà plastiche permettono la formatura; quarzi, che aiutano a mantenere la forma in cottura; feldspati, che favoriscono la fusione delle argille e quindi vengono usati per ridurre la temperatura dei forni. A questi si aggiungono eventuali additivi chimici che servono al modellamento. La quantità e il tipo di materie prime determinano la composizione e il colore del corpo ceramico. A seconda delle proporzioni di argilla (rossa perché contiene ferro) e di caolino (bianco), il corpo ceramico può essere da rosso-bruno, come le terrecotte, a bianco, come le porcellane. Dal giusto dosaggio dei componenti non dipende solo il colore, ma anche le caratteristiche e le resistenze del prodotto finito. È molto importante calcolare le giuste proporzioni delle materie prime, tenendone in considerazione sia le caratteristiche fisiche sia le proprietà chimiche. Tutte queste caratteristiche danno origine a tipologie di prodotti ceramici anche molto diverse tra loro: dai mattoni in laterizio alle lame dei coltelli più in voga del momento.
La preparazione del corpo ceramico
La piastrella è sempre composta da una base, detta corpo ceramico. Talvolta questo corpo può essere rivestito con uno smalto. La decorazione a stampa è parte di questo rivestimento. Sia il corpo ceramico che il rivestimento vengono realizzati con impasti di materie prime minerali, che poi vengono cotti perché si possano fondere insieme. La prima operazione da compiere quindi è determinare la ricetta: le materie prime che servono per comporre il corpo vanno scelte, pesate e mescolate. Poi vanno macinate in mulini a biglie: l’obiettivo è ottenere sospensioni perfettamente miscelate dalla granulometria controllata e omogenea. Più omogenea è la dimensione delle particelle, più semplice sarà il successivo processo di formatura. Ogni tanto per migliorare la miscelazione di un lotto (batch) è necessario aggiungere acqua. Questo processo è chiamato macinazione a umido e la miscela liquida che ne risulta slurry o slip. L’acqua in eccesso viene filtrata e lo slurry viene pompato in un essiccatore. Le gocce semiliquide vengono riscaldate da una colonna di aria calda, formando piccoli grani di dimensioni e forme controllate. La macinazione può avvenire anche a secco. In questo caso la granulazione avviene in un secondo momento: viene aggiunta acqua agli ingredienti già macinati e lo slurry viene quindi spruzzato in un flusso di aria calda ad alta pressione e velocità che lo essicca e ne atomizza il contenuto solido.
Piastrelle per rivestimenti
Piastrelle pressate a secco e smaltate con porosità alta. Possono avere una cottura singola o doppia (biscotto). Usate soprattutto per muri interni. Solitamente hanno forma rettangolare o quadrata, da 10×10 a 35×70 cm.
Piastrelle per pavimenti
Piastrelle con porosità media o bassa. Il corpo, in gres porcellanato, vetrificato o smaltato, può andare dal bianco all’ocra e fino al marrone scuro; ha una grana fine e omogenea. La finitura dello smalto può essere lucida o opaca. Usate per pavimenti interni. Alcuni modelli, resistenti al gelo, al ghiaccio e all’abrasione, possono essere usati anche per esterni. Solitamente quadrate, le misure vanno da 30×30 a 90×90 cm.
Gres porcellanato
Piastrelle pressate a secco e cotte una sola volta, con porosità bassa. Possono essere smaltate o meno. Sono generalmente squadrate. I formati standard vanno dai 15×15 ai 60×120 cm.
Lastre
Lamine ceramiche pressate senza usare forme tradizionali e cotte in forno a rulli. Sono entrate da poco nel mercato. Usate per pavimentazioni esterne, muri esterni, o in locali industriali. Estremamente sottili (3-5 mm) e flessibili, vengono prodotte in grandi dimensioni, fino a 160×480 cm.
La formatura e l’essiccazione
Alla polvere prodotta dall’atomizzatore a questo punto deve essere data una forma. La formatura può avvenire in diversi modi: le piastrelle di solito vengono pressate, e in alcuni casi estruse. Nel primo caso, grani vengono pressati spesso a secco, così che assumano la forma, la misura e lo spessore desiderati. La polvere, ancora umida perché contiene un legante organico o acqua, passa da una tramoggia a uno stampo liscio oppure lavorato. In questo caso la superficie della piastrella non sarà piana, ma avrà quella che si chiama “struttura”, ovvero una texture tridimensionale. Le presse sono tra i macchinari più dispendiosi dell’intero processo ceramico, in termini di energia: basta pensare che una pressa isostatica esercita sulla piastrella una pressione di oltre 10.000 kN, cioè fino a 480 kg/cm². Viene applicata in modo uniforme in tutte le direzioni, così da ridurre la possibilità che si creino microfratture e difformità di densità. Di recente sta prendendo piede un altro tipo di pressa, a nastro, meno energivora dell’altra. Il soffice viene fatto passare fra due nastri che lo compattano progressivamente fino a quando raggiunge lo spessore voluto. Con questo processo si ottengono lastre di grandi dimensioni, che vengono tagliate successivamente, prima o dopo la cottura. Dalla pressa, isostatica o a nastro che sia, esce la lastra ancora umida: va asciugata gradualmente in essiccatoi continui a tunnel o verticali, per evitare che si formino crepe. L’essiccazione può richiedere diverse ore.
La smaltatura
A questo punto la piastrella è pronta per essere smaltata: il rivestimento deve essere perfettamente coprente e omogeneo. Per questo è fondamentale trovare la ricetta dello smalto che si combini perfettamente con la tecnica di smaltatura usata: bisogna calibrare attentamente pigmenti e legante (binder). Il procedimento per preparare lo smalto è simile a quello che serve a preparare il corpo ceramico: vengono calcolate le quantità di materie prime necessarie per ricoprire un lotto, che poi vengono pesate, mescolate e macinate a umido o a secco. Per ottenere la giusta viscosità viene quindi aggiunto un legante, solitamente a base acquosa. Ci sono vari modi per applicare lo smalto: con il metodo a centrifuga o a disco viene applicato con un disco rotante che lo rovescia sulla superficie; con il metodo a vela viene fatto cadere sulle piastrelle che passano su un nastro trasportatore; può essere anche spruzzato con un aerografo. Infine, lo smalto può essere applicato anche con teste di stampa inkjet studiate per eiettare grandi quantità di materiale (abrasivo, ovviamente, dato che è composto da particelle minerali in sospensione) ad alta frequenza, senza rovinarsi e garantendo una copertura perfetta. Questa soluzione tecnologica non è ancora pienamente efficace: si sta ancora studiando e provando. Esiste anche la smaltatura a secco: vengono applicate sulla superficie della piastrella smaltata a umido polveri, fritte sminuzzate (materiali vetrosi) e smalti in grani. Dopo la cottura, le particelle di smalto fondono l’una nell’altra e danno origine a una superficie simile al granito.
La decorazione analogica e digitale: inchiostri e stampanti
A questo punto del processo la piastrella può essere decorata in modo analogico o digitale. Nel primo caso viene usata la tecnica serigrafica o quella a rullo: gli inchiostri vengono fatti passare attraverso un telaio grazie a una racla o fatti aderire a rulli in silicone che li trasferiscono quando toccano la piastrella. Nel secondo caso viene usata una stampante inkjet caricata con inchiostri a pigmento ceramico.
In entrambi i casi è cruciale la formulazione degli inchiostri, che sono molto diversi da quelli usati nelle arti grafiche. Innanzitutto, i pigmenti sono più grandi e pesanti rispetto a quelle che compongono, per esempio, un inchiostro UV o a solvente. Per questo vanno tenuti alla temperatura corretta e costantemente in sospensione all’interno del legante, che di solito è a base solvente: nelle stampanti per la ceramica (come in quelle per il vetro) i contenitori di inchiostro possono avere degli speciali mulini (tipo le fruste da cucina) che agitano il contenuto. Anche all’interno della macchina il sistema di circolazione dell’inchiostro è fondamentale, così come quello di pulizia. In un processo industriale ad altissima produttività come quello ceramico, le stampanti migliori sono quelle che garantiscono la massima produttività: questo si traduce in velocità di stampa e capacità di eiettare grandi quantità di liquido, certo, ma anche in resistenza e solidità, rapidità di pulizia e facilità di manutenzione. In questo settore la definizione di stampa richiesta è mediamente più bassa rispetto ad altri settori: 360×360 dpi è considerata una risoluzione accettabile. Questo è dovuto anche al fatto che gli inchiostri ceramici hanno un’ulteriore grande differenza rispetto a quelli organici: devono subire un processo di cottura ad altissima temperatura per fissarsi al supporto. La cottura li trasforma in due modi: le gocce si fondono tra loro, perdendo un po’ di definizione, e anche il colore cambia a volte anche in modo sostanziale. Per questo motivo il lavoro di campionatura e gestione del colore, in questo settore, è di importanza assoluta.
Infine, bisogna tenere presente che gli inchiostri usati nelle ceramiche non seguono la quadricromia tipica delle arti grafiche (CMYK). I motivi sono diversi: un po’ perché è difficile realizzare questi colori e mantenerli dopo la cottura; un po’ perché tradizionalmente il gusto estetico legato alle piastrelle porta alla scelta di colori naturali, a imitazione di pietre e legni. Di fatto, in una stampante ceramica capita quindi spesso di trovare tutti i canali colore caricati con marroni e grigi. Le stampanti inkjet usate nel settore ceramico sono solitamente single pass: questo garantisce un’adeguata velocità di stampa. Le linee di produzione moderne lavorano su tre turni, ininterrottamente, sette giorni su sette. Per questo hanno una produttività molto alta: da 15.000 a 25.000 metri quadrati al giorno. Le velocità di produzione variano da un minimo di 10 metri al minuto (il minimo per le lastre) a un massimo di 70 metri al minuto (il massimo per le piastrelle da parete). La velocità della linea di produzione solitamente viene dettata dalla velocità della pressa. Il processo di decorazione inkjet è delicato: vanno controllate diverse variabili per limitare gli errori e le imperfezioni: il calore della superficie da decorare, la sua umidità, la presenza di polvere. Di una stampante per ceramica vanno considerati anche il sistema elettronico, che deve essere particolarmente performante, il RIP e il software di color management.
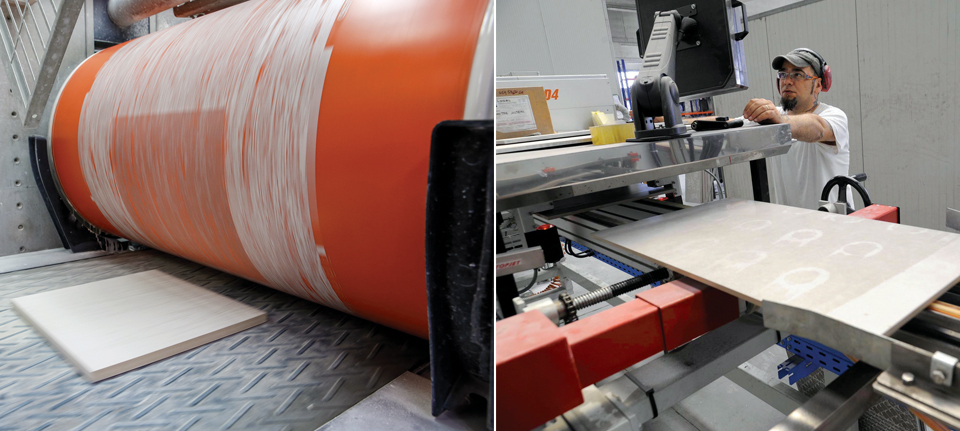
Le nuove tecnologie di smaltatura digitali nelle ceramiche sono integrate con quelle tradizionali (a sx). Il controllo qualità è una fase fondamentale del processo di lavorazione della ceramica (a dx). Foto: Greslab.
La cottura
Dopo la smaltatura e la decorazione, la piastrella deve essere scaldata intensamente per indurirsi e assumere la porosità e le resistenze desiderate. Per esempio, più alte sono le temperature di cottura e più impermeabile sarà la piastrella. Il processo di cottura è una delle fasi più delicate di tutta la lavorazione: se non viene gestita correttamente si rischia la rottura di interi lotti di produzione. Ogni ceramica custodisce i propri segreti di gestione del forno. Ricordiamo che la cottura può avvenire a temperature più basse rispetto a quelle normalmente richieste dai silico-alluminati di cui sono composte le argille grazie alla presenza di fondenti nell’impasto: non servono quindi 2.000°C, ma bastano dai 1.000 ai 1.300°C. La cottura delle piastrelle può essere singola o doppia. Quest’ultima tecnica, praticamente l’unica fino agli anni ’60, è ormai poco diffusa in Italia perché dà origine a prodotti ceramici di qualità inferiore. Viene usata ogni tanto per le piastrelle preparate con macinazione a secco, usate per i rivestimenti: vengono cotte una prima volta a bassa temperatura prima di essere smaltate e cotte nuovamente. La prima cottura, chiamata “biscottatura”, avviene a circa 1.000°C e rimuove le sostanze volatili dal materiale ed evita che si ritiri, che si restringa. Il prodotto di questa prima cottura è detto “biscotto”, e viene quindi cotto nuovamente a circa 950°C insieme allo smalto in un processo chiamato “gran fuoco”. Entrambe le cotture hanno luogo in forni continui, detti anche “forni continui a rulli”. Le piastrelle che richiedono la monocottura sono le più diffuse e solitamente sono preparate con macinazione a umido. In questo caso vengono usati forni a rulli, al cui interno le piastrelle si muovono su un nastro trasportatore. I tempi di cottura in questi forni possono essere anche molto brevi: possono bastare dai 30 ai 50 minuti a temperature che vanno dai 1.060 ai 1.250°C. Prodotti complessi che prevedono l’applicazione di lustri, oro o platino possono subire anche due o tre cicli di cottura a diverse temperature: la cottura che prevede l’applicazione di questi materiali nobilitanti si chiama “terzo fuoco”.
Il processo di cottura della piastrella ceramica in gres porcellanato è molto complesso, ed è ciò che permette la trasformazione delle materie prime (argille, feldspati e quarzi). A circa 100°C evapora l’acqua, a 500°C viene eliminata anche l’acqua contenuta nelle argille. A 800°C il caolino si trasforma in metacaolino, che poi diventa spinello e mullite primaria. A più di 900°C i feldspati si fondono: il composto ora è vetroso, fluido, viscoso e reagisce con il quarzo. A circa 1.050°C avviene la prima riprecipitazione e il silicio alluminato si trasforma in mullite secondaria. A 1.200°C l’impasto è viscoplastico, malleabile: a questo punto può iniziare il raffreddamento, e quindi l’indurimento. La mullite secondaria riprecipita. Sotto i 550°C avviene la transizione vetrosa: è una fase delicata, il materiale diventa rigido e fragile. Per questo bisogna rallentare il raffreddamento, così da evitare la rottura per shock termico. Le piastrelle vengono fatte stazionare in una zona del forno, oppure, se sono in un forno tunnel, vengono raffreddate in modo controllato. Quest’ultimo tipo di forno può essere lungo diverse decine di metri (fino a 100), oppure può sfruttare una logica multipiano. A questo punto le piastrelle vengono raffreddate progressivamente, fino a raggiungere la temperatura ambiente.
Il taglio e il controllo qualità
Nel caso in cui le piastrelle prodotte siano di grandi dimensioni, a questo punto può avvenire il processo di taglio. Viene fatto con la stessa strumentazione che viene adottata nel mondo dei materiali lapidei: macchine dotate di dischi diamantati che tagliano le piastrelle della dimensione desiderata. A questo punto vengono fatti i test che servono a verificare le resistenze e la qualità dei prodotti. Le piastrelle devono rispecchiare gli standard definiti dalla normativa UNI EN 14411:2016 Piastrelle di ceramica – Definizioni, classificazione, caratteristiche, valutazione e verifica della costanza della prestazione e marcatura, che definisce i termini e specifica le caratteristiche per le piastrelle di ceramica prodotte con estrusione e pressatura a secco, usate per pavimentazioni interne, esterne o pareti. Se lo fanno e superano i test, vengono ordinate, classificate, imballate e spedite in tutto il mondo. Pronte per diventare una parte fondamentale della vita di tutti noi. La ceramica è una certezza, dal Neolitico in poi.
Atomizzatore: strumento usato per nebulizzare ed essiccare sospensioni liquide.
Atomizzazione, essiccazione o spray-drying: processo di nebulizzazione ed essiccamento di sospensioni liquide.
Bicottura: quando il green viene sottoposto a una doppia cottura, prima e dopo la smaltatura. Può essere “rapida”, con entrambi i cicli termici inferiori a un’ora, oppure “lenta” o “tradizionale”, in cui entrambi i cicli sono di alcune ore.
Biscottatura: la prima cottura di alcuni prodotti ceramici. Le piastrelle che risultano da questa lavorazione hanno resistenze basse, per questo è ormai poco diffusa in Italia.
Biscotto: semilavorato poroso, non ancora smaltato, che risulta dalla prima cottura a temperature relativamente basse (750-950°C).
Biscuit: porcellana non verniciata che prevede una duplice cottura ad alte temperature (1.300°).
Body o corpo ceramico: la parte non superficiale della piastrella, il supporto che può essere decorato con smalto e stampa.
Compattato: il primo prodotto che risulta dalla formatura: è composto di polveri.
Corpo ceramico: v. body.
Formatura: viene condotta per pressatura idrostatica, pressatura a rulli, estrusione o colaggio. Nel caso delle piastrelle ceramiche i processi sono solitamente i primi tre.
Fritta: pasta vetrosa che si forma dalla fusione di silicati, borati, fluoruri e feldspati; macinata, è usata per la preparazione di rivestimenti vetrosi.
Glaze, rivestimento o smalto: l’involucro che toglie la permeabilità alle paste tenere, dà levigatezza a quelle dure, ricopre il corpo delle argille colorate; può essere trasparente o colorato.
Granulazione: processo di trasformazione da slurry a grani pronti per la formatura. Avviene in un atomizzatore.
Greificazione: sinterizzazione del gres porcellanato: nella cottura di questo materiale precede la fusione e consiste nella saldatura dei granuli fra loro; aumenta la resistenza meccanica e l’impermeabilità del pezzo.
Gres: ceramica caratterizzata da un impasto colorato e compatto ottenuto usando argille con un basso punto di fusione.
Granfuoco o grande fuoco: la seconda cottura della ceramica. Cottura ad alta temperatura delle decorazioni dipinte o stampate con colori non fusibili su coperte o smalti crudi. Procedimento ormai obsoleto.
Green o verde: il compatto di sufficiente resistenza che si ottiene dalle miscele secche o umide pressate.
Lustro: tecnica decorativa che permette di ottenere il color oro o rubino con sfumature cangianti o iridescenti.
Monocottura: quando il corpo ceramico e il rivestimento sono sottoposti insieme a un’unica cottura.
Mulino a biglie, a palle o a sfere: strumento usato per macinare materiali in polvere finissima; riempito di biglie di ceramica, funziona con un movimento rotatorio generalmente orizzontale.
Porcellana: ceramica con un impasto bianco e compatto a base di caolino e feldspato cotto a temperatura molto alta (1.200-1.400°C).
Porosità: rapporto tra la somma dei volumi di cavità, fessure e spazi intergranulari di un materiale e il suo volume totale. È quasi assente nel gres e nella porcellana.
Ritiro: variazione dimensionale della piastrella; può avvenire con la cottura, ma va evitata il più possibile.
Rivestimento: v. glaze.
Sinterizzazione: processo di densificazione di un compatto di polveri: la porosità interstiziale scompare e le particelle adiacenti si uniscono. Avviene nella terza fase della cottura.
Slip o slurry: sospensione liquida che si produce mescolando acqua agli ingredienti del corpo ceramico; viene sottoposta alla macinazione a umido con un mulino a biglie.
Smalto: v. rivestimento.
Terzo fuoco: la cottura che serve a fissare i lustri, le dorature o le argentature; il nome deriva dalla bicottura, della quale era il proseguimento. Oggi il terzo fuoco può avvenire anche direttamente dopo la monocottura.
Tramoggia: apparecchio costituito da un recipiente a pareti inclinate con un’apertura sul fondo chiusa da uno sportellino; usato per scaricare materiali incoerenti, è applicato a vari tipi di macchine.
Verde: v. green.