Il termine automazione nasce nei primi anni Cinquanta del Novecento e faceva già allora riferimento alle innovazioni tecnologiche in grado di snellire il lavoro umano e velocizzare e aumentare la produttività di una qualsiasi azienda. Innovazioni tecnologiche che andavano ad affiancare o addirittura a sostituire attività umane ripetitive, poco qualificate e spesso pericolose.
Le radici dell’automazione si intrecciano con lo sviluppo tecnologico e con l’ambizione umana di migliorare sempre i processi e i risultati produttivi di un’azienda. Ma anche con la paura che le macchine possano arrivare a sostituire l’attività umana nei processi industriali, con conseguente perdita di posti di lavoro. Oggi il timore è nei confronti dell’intelligenza artificiale, delle reti internet mobili di quinta generazione, delle analisi e utilizzo dei big data e della tecnologia cloud. Queste quattro innovazioni tecnologiche (AI, 5G, big data e cloud) sono quelle che uno studio del World Economic Forum (fondazione senza fini di lucro nata nel 1971 con sede in Svizzera), intitolato The future of jobs e pubblicato a fine 2018, definisce come i driver che “sono destinati a dominare il periodo 2018-2022 influendo positivamente sulla crescita del mercato mondiale”.
Il report del World Economic Forum
Secondo il report del WEF entro il 2022, secondo le previsioni di investimento delle aziende, l’85% del panel di riferimento dell’indagine (condotta tra i principali funzionari delle risorse umane e i dirigenti d’azienda di 12 settori in 20 economie sviluppate ed emergenti, che rappresentano collettivamente il 70% del Pil globale) afferma di avere intenzione di aumentare il loro utilizzo e analisi dei big data e di voler adottare nuove tecnologie come l’internet of things e fare un maggiore uso del cloud compunting. Un po’ meno convinta la spinta ad investire in robot, con percentuali a seconda del settore produttivo che vanno dal 23 al 37% di aziende intenzionate a investire in robot, droni o altre macchine intelligenti che replichino il lavoro umano. Nei prossimi cinque anni circa la metà delle imprese intervistate dichiara di aspettarsi una riduzione della manodopera a tempo pieno a causa dell’automazione, stando alle competenze odierne della propria forza lavoro. Tuttavia, il 38% delle aziende prevede altresì di estenderla a nuovi ruoli nei processi produttivi, e più di un quarto si aspetta che l’automazione porti alla creazione di nuovi ruoli nella propria azienda. E se milioni di posti di lavoro nei prossimi anni andranno persi perché sostituiti dalle macchine e dall’automazione dei processi, molti di più se ne creeranno, perché ci sarà bisogno di chi quelle macchine sia in grado di gestirle. Il WEF quantifica queste perdite e questi guadagni in 75 milioni di professionalità distrutte dall’introduzione di intelligenza artificiale e robot, 133 milioni quelle create per gli stessi motivi, con un saldo netto di 58 milioni di posti di lavoro in più in tutto il mondo. Si tratta di una stima, ma quel che è certo che ci saranno nuovi lavori, come quelli (di difficile traduzione dall’inglese) di data analyst and scientist, di software and applications developer, di ecommerce and social media specialist.
Come fronteggiare il cambiamento?
In Italia nel 2018 sono salite “dal 12,9% al 16,9% le imprese che investono in competenze digitali provvedendo alla formazione dei propri addetti”. Lo afferma un report dell’Istituto nazionale di statistica (Istat) dal titolo Cittadini, imprese e ICT e riferito all’anno 2018 (l’indagine della situazione del 2019 è tutt’ora in corso). La ricerca testimonia un ampio divario tra grandi e piccole imprese nel livello di digitalizzazione: livelli alti o molto alti sono presenti nel 44% delle imprese con almeno 250 addetti e solo nel 12,2% delle imprese da 10 a 49 addetti. Sempre più le aziende che dichiarano di aver difficoltà a trovare professionalità preparate per coprire questo tipo di ruoli, tanto che il 60% ha dichiarato ricorrere a personale esterno per queste attività.
Appena più premettente sembra il quadro degli investimenti delle imprese italiane in quelle che il report Istat definisce come “tecnologie emergenti”, fra le quali il già citato cloud compunting, software per l’analisi dei big data e la robotica. In termini generali le grandi imprese mostrano una propensione superiore o in linea con la media europea nell’analisi di big data (il 30% contro il 25% dell’Ue28), nell’uso di stampanti 3D (13%, in linea con la quota dell’Unione europea) e della robotica (un punto percentuale maggiore rispetto al 25% del resto d’Europa) – questi ultimi due, ambiti introdotto per la prima volta nel questionario nel 2018.
A concentrarsi sull’analisi dello sviluppo tecnologico delle imprese in Italia è anche il Rapporto 2019 dal titolo Dove va l’industria italiana del Centro Studi di Confindustria. L’ultima parte dello studio si focalizza sulle industrie manifatturiere in Italia, affermando come la trasformazione digitale delle imprese debba essere sostenuta attivamente attraverso “tre ambiti fondamentali: 1) gli investimenti in tecnologie; 2) un più stretto legame tra mondo della ricerca e l’industria attraverso il rafforzamento dei meccanismi di trasferimento tecnologico; 3) la formazione a tutti i livelli: la disponibilità di competenze e di profili professionali capaci di progettare e gestire l’integrazione delle tecnologie 4.0 rappresenta infatti la chiave per l’innovazione digitale”, si legge nel rapporto.

Fabbrica di cioccolato industriale con mano robotizzata automatica
Cosa si sta facendo
Per non perdere la sfida dell’innovazione tecnologica al tavolo con Asia e Stati Uniti, l’Europa è corsa ai ripari varando il piano Digitising European Industry – Reaping the full benefits of a Digital Single Market, lanciato nell’aprile del 2016. La Commissione ha messo in campo misure specifiche con l’obiettivo di rafforzare la competitività dell’industria europea attraverso lo sviluppo e l’integrazione delle tecnologie digitali nei processi produttivi. Si sta lavorando anche alla definizione del programma di finanziamento Digital Europe, il primo interamente dedicato all’economia digitale. Sarà contenuto nel prossimo bilancio per il periodo 2021-2027 e supporterà la trasformazione digitale delle società e delle economie europee attraverso l’implementazione su vasta scala delle tecnologie digitali. La proposta è di destinarvi 9,2 miliardi di euro per finanziamenti a progetti relativi a cinque aree tematiche: supercalcolo, cybersecurity, competenze digitali avanzate, utilizzo delle tecnologie digitali in tutti gli ambiti economico-sociali e intelligenza artificiale (AI). Ma finanziare e investire in ricerca non basta, perché “sostenere solo l’offerta di soluzioni tecnologiche 4.0 esporrebbe infatti le imprese che investono in ricerca al rischio di non trovare un mercato attrezzato ad assorbire le innovazioni tecnologiche nel frattempo sviluppate, e quindi di non essere in grado di ripagare gli sforzi finanziari necessari alla loro realizzazione”, si legge del documento di Confindustria. È per questo che gli Stati dell’Unione europea nel corso degli ultimi anni si sono attrezzati per sostenere l’adozione delle nuove tecnologie da parte delle piccole e medie imprese. In Italia lo si è fatto con il Piano nazionale Impresa 4.0.
L’Industria 4.0 è l’insieme di innovazioni e “ammodernamenti” applicabile ai processi industriali e che tende al raggiungimento una produzione industriale automatizzata, interconnessa e digitalizzata, in grado di garantire una maggiore, più flessibile e più veloce attività. Stando ai dati Istat, circa l’86% delle imprese con almeno 10 addetti non investe, il 13,7 che ha dichiarato di aver già investito nel biennio 2016-2017 e il 13,3% afferma di volerlo fare da qui al prossimo anno. In Italia a sostenere lo sviluppo di Industria 4.0 c’è il Piano nazionale Impresa 4.0 che prevede misure concrete per le aziende che vogliano investire in innovazione.
Come funziona:
Dall’1 gennaio 2019 al 31 dicembre 2019 il bene viene acquisito, installato, collaudato, interconnesso. Viene esteso fino al 31 dicembre 2020 a condizione che entro la data del 31 dicembre 2019 il relativo ordine risulti:
- accettato dal venditore
- sia avvenuto il pagamento di acconto in misura pari ad almeno il 20% del costo di acquisizione.
Iperammortamento
La legge di bilancio 2019 prevede una rimodulazione degli incentivi sugli investimenti complessivi aziendali. La maggiorazione del costo di acquisizione degli investimenti si applica nella misura:
- del 170% fino a 2,5 milioni
- del 100% tra 2,5 e 10 milioni
- del 150% tra 10 e 20 milioni
- Nessun beneficio per la quota che eccede i 20 milioni
Superammortamento
La misura viene prorogata solo per investimenti effettuati da 1 aprile 2019 al 31 dicembre 2019 (fino al 30 giugno 2020 con ordine entro il 31/12/2019 e pagamento di almeno il 20% del costo totale come acconto) (Decreto Crescita).
Il manifatturiero e l’iper-ammortamento
Sulla base delle dichiarazioni dei redditi delle società di capitali italiane per l’anno d’imposta 2017, l’ultimo disponibile, la stima ex-post preliminare dell’ammontare degli investimenti realizzati risulta pari a 5 miliardi per i beni d’investimento materiali e 3,3 miliardi per i beni d’investimento immateriali in circa 8 mila imprese per la componente iper-ammortamento sui beni materiali e in circa 18 mila imprese per la componente iper-ammortamento sui beni immateriali. Dati che, afferma Confindustria, “devono tuttavia essere considerati a tutti gli effetti una sottostima, anche significativa, del dato reale sugli investimenti in tecnologie digitali. La ragione principale è che una quota rilevante di imprese non è riuscita a ricevere e a interconnettere i beni strumentali ordinati nel corso del 2017 entro il 31 dicembre di quello stesso anno, ed è quindi stata costretta a posticipare alla successiva dichiarazione dei redditi l’inclusione dei relativi costi deducibili”. Per arrivare ai 10 miliardi di stima prima citati si sono integrate le informazioni relative alla dichiarazione dei redditi con quelle degli ordini non evasi nel corso dell’anno. Sono state oltre 4.400 le imprese manifatturiere che hanno fruito dell’iper-ammortamento sull’acquisto di beni strumentali materiali, per un ammontare investito stimato di oltre 4 miliardi e 250 milioni di euro, che corrispondono all’86% circa del totale. Sono molto diverse le cifre di investimento a seconda del comparto manifatturiero che si prende in considerazione. Confindustria stila una sorta di classifica che include 23 comparti manifatturieri considerati per l’investimento medio per impresa. Sia il settore della carta che quello della stampa, il primo per un totale di 112 aziende con un investimento medio ciascuna di due milioni e 26 mila euro e il secondo di un milione e 64 mila euro per ciascuna delle 127 aziende risultanti, rientrano nelle prime dieci posizioni di questo elenco che illustra l’alta variabilità settoriale nell’investimento medio. Investimento medio la cui entità varia, come è ovvio, a seconda delle dimensioni dell’azienda: 117 mila euro per imprese fino ai 9 dipendenti; 412 mila euro per imprese con unità di addetti comprese tra 10 e 50; 1 milione e 384 mila euro per imprese con unità di addetti comprese tra 51 e 250; 5 milioni e 400 mila euro per le imprese con più di 250 dipendenti.
L’automazione nell’industria della stampa
Al tavolo degli incontri di questi primi mesi di attività dei DIH c’era anche la Federazione Carta e Grafica che rappresenta i comparti industriali di Acimga (macchine per la grafica e cartotecnica), Assocarta (carta e cartone) e Assografici (grafica e cartotecnica, trasformazione), con Unione Grafici di Milano e Comieco quali soci aggregati, e che ha voluto procedere a un “Check-up Industry 4.0”, in collaborazione con SDA Bocconi. Si tratta di un primo tentativo di capire in che modo stiano reagendo le aziende del comparto: l’indagine è stata condotta tra dicembre 2017 e marzo 2018 fra le aziende facenti parte Federazione Carta e Grafica, e il totale dei rispondenti validi (108 su 774) rappresenta un campione pari al 14% della popolazione indagata. Dal report pare emergere “una chiara tendenza: seppur con un certo ritardo complessivo la filiera si sta muovendo, anche grazie alle sollecitazioni associazionistiche e confindustriali in genere, verso la creazione delle condizioni strutturali per poter poi cogliere appieno i vantaggi e le opportunità offerte dalla trasformazione paradigmatica in atto”, si legge nello studio. Secondo quanto emerge dall’indagine, “i settori che presentano una dinamica abbastanza comparabile e favorevolmente orientata all’abilitazione dello scenario 4.0 sono quelli dei grafici e cartotecnici e dei produttori di macchine. Decisamente più timido è l’orientamento mostrato dai produttori di carta che, probabilmente per la natura dei loro processi manifatturieri (…) non ritengono possibile allo stato attuale, particolarmente cruciale per lo sviluppo industriale a medio termine del comparto, un incremento della gestione e dell’elaborazione dei dati raccolti lungo tutta la sua catena del valore”. Per quel che riguarda i produttori di macchine, l’indagine rileva come “l’attenzione all’investimento nelle tecnologie 4.0 per il triennio successivo sia particolarmente concentrata sulla gestione della macchina in opera presso la clientela. I produttori di macchine sottolineano l’importanza di ridurre il total cost of ownership del loro impianto, sia perché se ne riducono ulteriormente i consumi energetici, sia per la possibilità di assistere a distanza, diagnosticare predittivamente guasti e malfunzionamenti e tracciare l’intero ciclo di produzione allo scopo di offrire un migliore servizio al cliente e ridurre drasticamente i suoi fermi-macchina e i costi di manutenzione in genere”. Le aziende di stampa vivono “come particolarmente cruciale il tema della gestione della commessa e della comunicazione trasparente e continua con il committente. In ragione di ciò, assegnano priorità massima in ordine all’interesse sulle tecnologie al tema dei software per la gestione dei progetti intra e inter-company. (…) Diametralmente opposto risulta l’interesse alle tecnologie di ‘comunicazione’ e di ‘trasmissione’ (RFID, NFC, inchiostri intelligenti e nanotecnologie in genere). Tuttavia, è anche da rilevare che tale interesse emergerebbe con maggiore enfasi se il mercato di sbocco mostrasse maggiore propensione tecnologica. Anche per questo l’editoria e la stampa commerciale risultano ancora molto incerti in ordine all’utilizzo e alla convergenza delle tecnologie”, si legge nel rapporto.
Il network dell’innovazione 4.0 è costituito dai soggetti istituiti dal Piano Nazionale per procedere alla sensibilizzazione delle imprese sul tema e favorire l’avvio di progetti di digitalizzazione del sistema produttivo. Si tratta dei Competence Center (CC) e dei Digital Innovation Hub (DIH). Entrambi si inseriscono nell’ambito del piano Digitising European Industry varato dalla Commissione europea nel 2016 citato in precedenza. I DIH sono strutture che offrono alle imprese la possibilità di avvicinarsi alle tecnologie 4.0, di comprenderne le possibilità applicative; i CC rappresentano il luogo dove le imprese possono concretamente conoscere e testare le tecnologie e dove possono trovare supporto tecnico per la loro applicazione. In Italia ci sono otto Competence center, i DIH fanno invece parte di una rete creata da Confindustria, che ha avviato un confronto con le Associazioni territoriali di categoria per creare delle “porte d’accesso” al mondo di Industria 4.0. Ce ne sono 22 in tutta Italia e nel primo anno di operatività hanno realizzato oltre 400 iniziative tra seminari, incontri one-to-one e visite studio, e hanno realizzato oltre 600 test di valutazione della maturità digitale con l’analisi dei processi aziendali per stabilire il livello di digitalizzazione delle imprese, si legge nel report. “Per supportare i DIH nell’attività di orientamento, Confindustria ha siglato accordi di collaborazione con il Centro Tecnologico e Applicativo di Siemens, con HP e Google, rispettivamente dedicati alla stampa 3D e all’intelligenza artificiale”, conclude il documento.
L’avanzata dei cobot
Sistemi robot e cobot (il co-robot, robot collaborativo, è concepito per interagire fisicamente con l’uomo in uno spazio di lavoro, diversamente da quelli progettati per operare in maniera autonoma o con una guida limitata) sono sempre più l’investimento cui si affacciano le piccole medie imprese che compongono il tessuto industriale e manifatturiero italiano. L’aumento dei costi di produzione nelle aziende e la conseguente riduzione dei margini, la scarsità di manodopera specializzata e le esigenze sempre più sofisticate e variegate dei consumatori, rendono queste soluzioni di automazione un acquisto interessante anche per le piccole aziende.
«È conveniente per tutte le Pmi che ritengono di automatizzare un processo che, in quel momento, o viene svolto manualmente, oppure con macchinari di altro genere, ma non genera i risultati sperati in termini di resa ed efficienza», spiega Alessio Cocchi, Country manager Italia di Universal Robots, azienda specializzata nella tecnologia robotica collaborativa fondata in Danimarca nel 2005 da Esben Østergaard, Kasper Støy e Kristian Kassow, e che nel 2018 ha registrato un volume d’affari di 234 milioni di dollari. «Quando la Pmi decide di implementare i cobot si accorge di due tipologie di vantaggi misurabili non appena entrano in azione. Da un lato l’automazione genera per definizione un aumento di produttività e induce “coerenza qualitativa” nei prodotti realizzati. Dall’altro produce “vantaggi indiretti” che differenziano questo tipo di strumento di lavoro, il cobot appunto, da altri – prosegue Cocchi -. Dimensioni ridotte e l’opportunità di lavorare senza barriere protettive equivalgono alla riduzione del layout produttivo impegnato dall’automazione stessa, generando un diretto vantaggio economico. Le medesime caratteristiche, inoltre, ne consentono un rapido spostamento su fasi di lavoro diverse rispetto a quella sulla quale vengono inizialmente impiegati, inserendo flessibilità operativa e applicativa all’automazione e all’azienda in generale. A questi si aggiungono altri vantaggi legati, ad esempio, a una migliore ergonomia per le postazioni di lavoro degli operatori o a un loro spostamento verso fasi a maggior valore aggiunto, liberandoli da operazioni ripetitive, noiose e/o talvolta pesanti/usuranti. Non esiste quindi un limite oggettivo superato il quale il cobot genera vantaggi. Esistono limiti costruttivi, in termini di sbraccio e payload, per cui i cobot non possono fare qualsiasi tipo di operazione (come ogni altra macchina, peraltro). Se, tuttavia, questi vengono utilizzati sfruttandone le caratteristiche sono portatori di vantaggi».
Un cobot della Universal Robots ha un costo “a listino” che va dai 25 mila ai 35 mila euro a seconda della “taglia”, spiega Cocchi, ma il costo dipende più che altro da quali operazioni il cobot deve svolgere, se è integrato oppure no a una linea o ad altre macchine etc, tanto che ogni applicazione viene sviluppata su misura per il cliente da parte dei system integrator o degli end user direttamente. «Se, tuttavia, un’azienda utilizza un cobot “da solo” oppure in integrazioni “semplici” allora diventa molto più semplice misurare il Roi. In casi come questi l’esperienza di UR è molto varia, ma si attesta attorno a un ritorno sull’investimento di sei mesi, toccando punte record straordinarie. Il nostro cliente Task For Tips ha misurato un Roi di appena 34 giorni – aggiunge Cocchi -. Zund è un nostro cliente e ha sviluppato un’applicazione in cui il cobot, in unico passaggio, effettua il picking delle stampe pretagliate e rimuove lo scarto. Un’applicazione semplice, ma che comporta un guadagno di efficienza notevole. Primo perché è un’operazione non presidiata, quindi l’operatore che prima se ne occupava è ora libero di dedicarsi ad altre, decisamente più importanti, attività. In secondo luogo perché il cobot è in grado di svolgere quelle operazioni in maniera più precisa e veloce – spiega Cocchi -. Da questa e da altre esperienze presso i nostri clienti direi che l’industria della stampa si sta approcciando al tema della robotica collaborativa con il giusto mix di aspettative e curiosità, per sondare fino a che punto i robot collaborativi possano realmente dare una svolta ai processi. L’industria della stampa è per noi un settore tutto sommato ancora nuovo in cui stiamo esplorando possibilità applicative. Se allarghiamo il discorso ad altre attività, come l’etichettatura, o tutte le attività di logistica e fine linea (picking, packing, pallettizzazione, assemblaggio) abbiamo diverse evidenze applicative che confermano i valori tradizionalmente legati ai cobot: efficienza, ripetibilità, precisione, possibilità integrative anche in layout ristretti e saturi, flessibilità», conclude Alessio Cocchi.
Due esperienze di integrazione: Zund e Mimaki
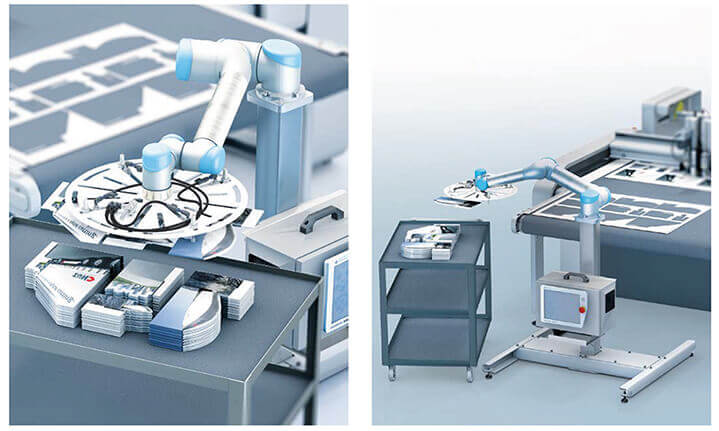
Il robot Pick & Place rimuove i pezzi tagliati dall’area di scarico del cutter Zund e li smista
L’esperienza di integrazione citata dal Country manager Italia di Universal Robots trova conferma nelle parole di Lia Mauri, general manager di Zund Italia, che afferma come i bracci robotizzati siano compatibili con i cutter digitali Zund G3 e S3, permettendo di evitare l’intervento umano nell’esecuzione di attività monotone e ripetitive, che per queste loro caratteristiche diventano molto spesso pericolose, come il carico e lo scarico delle stampe e la rimozione degli scarti. Al momento, dice Mauri, non ci sono ancora installazioni in Italia di una soluzione robotica integrata a una macchina Zund, ma il mercato comincia a esserne incuriosito. «Un nostro cliente di un’azienda cartotecnica si era detto interessato a questo tipo di investimento, ma è tutto ancora in divenire», spiega Mauri che aggiunge come l’azienda stia lavorando a una rete globale di conoscenze condivise sull’automazione, così da arrivare preparati a quando il mercato sarà davvero pronto per innovarsi radicalmente, anche in Italia. La timidezza dell’industria italiana all’approccio coi robot è testimoniata anche dai risultati dell’indagine del sopracitato report dell’Istat Cittadini, imprese e ICT riferito all’anno 2018, il primo per il quale sono state introdotte, nel questionario della rilevazione sottoposto alle imprese, domande relative all’utilizzo della robotica e della stampa 3D, indice di come queste tecnologie inizino ad avere una seppur minima rilevanza nell’industria tricolore. Laddove per robotica si intendono robot industriali, robot collaborativi interconnessi e programmabili, risulta che la utilizza l’8,7% delle imprese con almeno 10 addetti; tuttavia, nei settori dove i robot sono direttamente utilizzati a supporto dell’attività produttiva il peso del loro impiego aumenta, come nel settore della fabbricazione di mezzi di trasporto (41,4%) e tra le imprese con almeno 250 addetti del settore manifatturiero (circa 60%). Ma se la partenza sembra incerta, il settore è in continua evoluzione ed esperienze di integrazione fra robot e mondo della stampa si stanno lentamente costruendo in tutta Europa, puntando all’ottimizzazione del workflow per una maggiore efficienza dell’intero processo produttivo. È necessario che le macchine si integrino alla perfezione, “imparando” la sequenza di movimenti necessaria a movimentare pezzi o a qualsiasi altra funzione siano destinate. Un altro produttore che ci sta lavorando è Mimaki, che in Germania ha creato una linea di produzione di stampa a LED UV integrata e automatizzata. «Mimaki ha già abbracciato le innumerevoli possibilità dell’Internet of Things sviluppando sistemi di stampa avanzati in grado di comunicare con i robot, nonché con una vasta gamma di hardware tra cui nastri trasportatori, dispositivi di ispezione e macchine da taglio», afferma Uwe Niklas, general sales manager, Mimaki Deutschland GmbH, che continua: «L’obiettivo è quello di consentire ai fornitori di servizi di stampa di creare linee di produzione completamente connesse, consentendo in definitiva la produzione su richiesta in maniera automatica e la personalizzazione in grandi volumi». Nello specifico Mimaki ha collaborato con l’azienda tedesca Robominds (distributrice in Germania di Universal Robots), collegando a una Mimaki UJF-7151plus un braccio robotizzato in grado di caricare e scaricare i substrati dalla stampante senza alcun intervento umano. Lo scambio di informazioni tra la macchina e il cobot è abilitato da un’interfaccia basata su IoT Mimaki, denominata Job Controller IP. I vantaggi annunciati dall’azienda vanno dall’aumento della produttività e della capacità di stampa, alla flessibilità nella gestione dei materiali e alla riduzione dei tempi di avviamento della macchina.
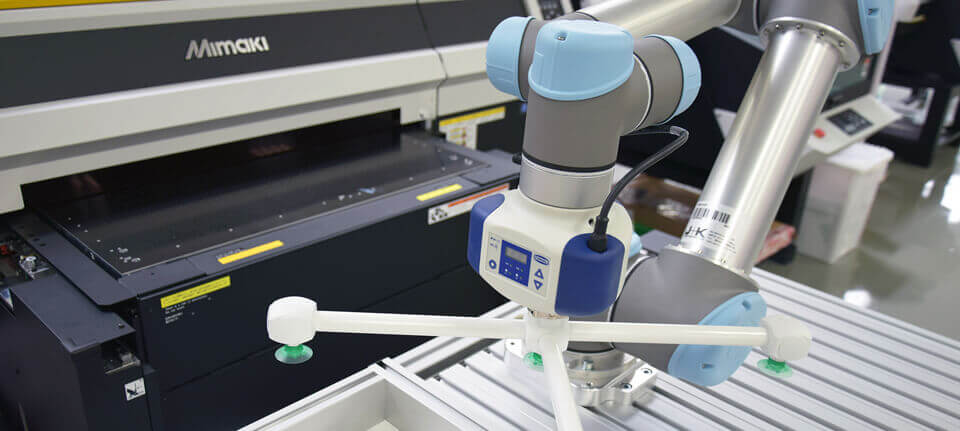
Una soluzione Robominds collegata a una Mimaki UJF-7151plus