Azienda storica italiana dalla forte spinta all’innovazione, Jannelli&Volpi progetta e realizza collezioni di carte da parati conosciute e apprezzate in tutto il mondo. Attraverso un processo produttivo articolato che – attingendo a un patrimonio storico di saperi tecnologici differenti e stratificati – affianca le tecniche di stampa tradizionali a soluzioni di ultima generazione.
È un luogo nel quale l’innovazione si intreccia con la tradizione e la produzione industriale coniuga creatività, know how artigianale e processi tecnologici di ultima generazione. Nei suoi laboratori, le idee prendono forma e diventano progetti creativi per poi trasformarsi, nei reparti di produzione e confezionamento, in rivestimenti murali capaci di dare nuovo respiro e diverse interpretazioni agli ambienti. È la ‘wallpaper factory’ di Jannelli&Volpi, specialista italiano di carta da parati e tessuti d’arredamento venduti in tutto il mondo: lo stabilimento di Sirpi di cui Jannelli&Volpi è capo gruppo ha aperto per la prima volta le porte per mostrare come nascono le collezioni dell’azienda, dal concept al prodotto finito. Attraverso un processo industrializzato che conserva una forte impronta umana, nel quale l’affiancamento della stampa rotativa alla tecnologia di stampa digitale consente di conseguire una flessibilità applicativa indispensabile per rispondere ai cambiamenti del mercato.
Tra know how storico e innovazione
Quella di Jannelli&Volpi è la storia di un’azienda italiana profondamente radicata nel territorio di appartenza che ha saputo crescere e affermarsi a livello internazionale, distinguendosi per capacità creativa e qualità. Fondata nel 1961 da Oreste Jannelli, insieme alla moglie e ai cognati, è oggi gestita dai tre figli Paola, responsabile CreativeLab e marketing&comunicazione, Mauro, presidente dell’azienda, e Lidia, responsabile finanziaria.
“Abbiamo un’eredità culturale legata al rivestimento murale di lunghissima data. L’esperienza della nostra famiglia nella gestione dell’attività e nello sviluppo del marchio costituisce un valore fondamentale: sia dal punto di vista del retaggio culturale sia dal punto di vista dell’appartenenza territoriale, la costruzione del nostro prodotto è 100% made in Italy”, racconta Paola Jannelli. “Si tratta di un aspetto fondamentale per una realtà come la nostra, che esporta il 90% della produzione: Jannelli&Volpi coltiva il proprio made in Italy nel modo più autentico, e tale valore è riconosciuto appieno dal mercato.”
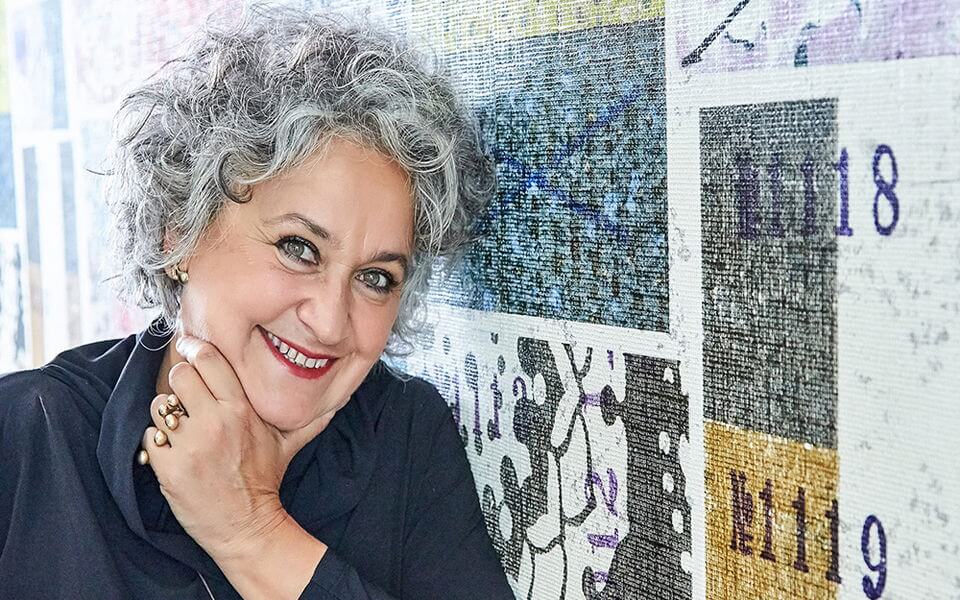
Paola Jannelli, alla guida dell’azienda insieme ai fratelli Mauro e Lidia, durante la visita alla wallpaper factory di Sirpi | foto L. Scaccini
Sotto la guida di un management incline a rinnovare costantemente la struttura operativa e le strategie di prodotto, Jannelli&Volpi ha vissuto un periodo di forte evoluzione. “Nel 2010 iniziarono i lavori di costruzione del nuovo stabilimento di Sirpi a Tribiano, alle porte di Milano, che oggi occupa un’area di 25mila metri quadrati (di cui la metà è edificata) e ospita, oltre alla produzione e alla logistica, anche uffici, reparti creativi e una zona destinata all’accoglienza dei clienti, o ‘editori’, ovvero quelle realtà che si appoggiano a noi per produrre le loro collezioni. Nello stesso periodo, la sede milanese di via Melzo fu trasformata nel concept store JVstore, realtà commerciale e luogo di ispirazione nonché spazio destinato a ospitare eventi e iniziative dedicati al décor.”
Sul fronte dell’offerta, il 2006 fu l’anno del lancio del progetto ‘wallpaper on demand’, che introdusse – attraverso la piattaforma WonD – la possibilità di ordinare online carte da parati personalizzate nei disegni e nelle dimensioni. A questo, seguirono altre pietre miliari: il lancio della prima collezione wallcovering Marimekko by Sirpi e del brand J&V Italian Design, rivolta al mercato internazionale, entrambe nel 2009; la presentazione, nel 2013, di Jwall tailor made, un servizio di personalizzazione delle linee standard – abilitato dalla stampa digitale; lo sviluppo delle collezioni Armani/Casa Exclusive Wallcoverings Collection, create in collaborazione con la maison Armani.
“Ci siamo posti l’obiettivo di presentare una nuova collezione ogni anno, oltre alle nostre e a quelle sviluppate per i clienti.” E se gli investimenti in tecnologia sono fondamentali per consentire all’azienda di raggiungere tale obiettivo, un ruolo altrettanto importante lo riveste la gestione lungimirante delle risorse umane. “Stiamo costruendo un team di giovani che occupano ruoli di responsabilità”, spiega Paola Jannelli. “Nella nostra struttura, il team dei ‘saggi’ si affianca al gruppo ‘primavera’, al quale è affidata la parte operativa. In questo modo, vogliamo garantire la continuità dell’azienda.”
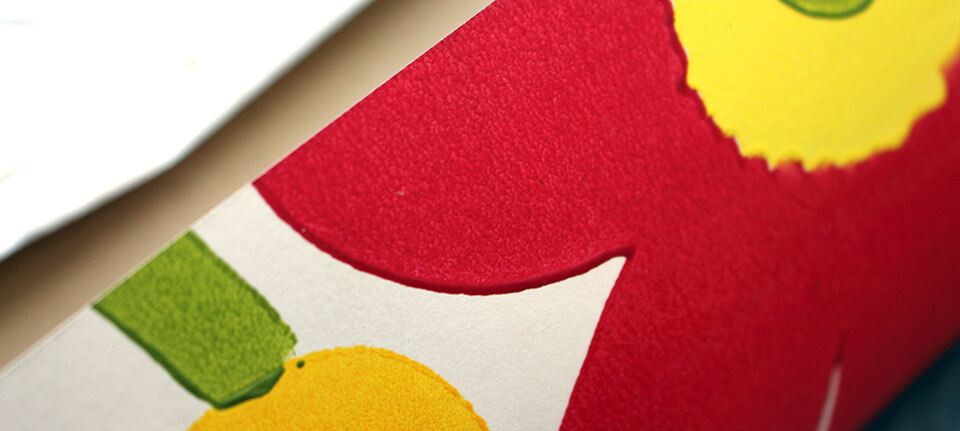
Lavorazione realizzata da Jannelli&Volpi | foto di Valeria Ghion
Nel cuore della produzione
Il processo produttivo delle carte da parati di Jannelli&Volpi comincia con la preparazione delle basi: nel reparto di spalmatura, uno strato di pvc viene applicato sulle bobine di carta e successivamente asciugato in un forno. “Nasce così la materia prima semilavorata. Dalla quantità di pvc applicata dipende la morbidezza del prodotto finito, mentre per ottenere una migliore saturazione cromatica in alcuni disegni o variazioni coloriamo direttamente anche il pvc”, spiega Paola Jannelli. Una volta pronte, le bobine passano nel reparto rotocalco, attrezzato con rotative, per essere decorate. “Facciamo incidere i cilindri sulla base dei disegni e, lavorando con sovrapposizioni a registro, riusciamo a ottenere diversi pattern ed effetti particolari e ricercati. La produzione minima in rotocalco è di 3 mila metri, le produttività raggiunte sono molto elevate.” La finitura del prodotto – realizzata nel reparto di goffratura – consiste nel creare il rilievo, per arricchire la texture della carta da parati.
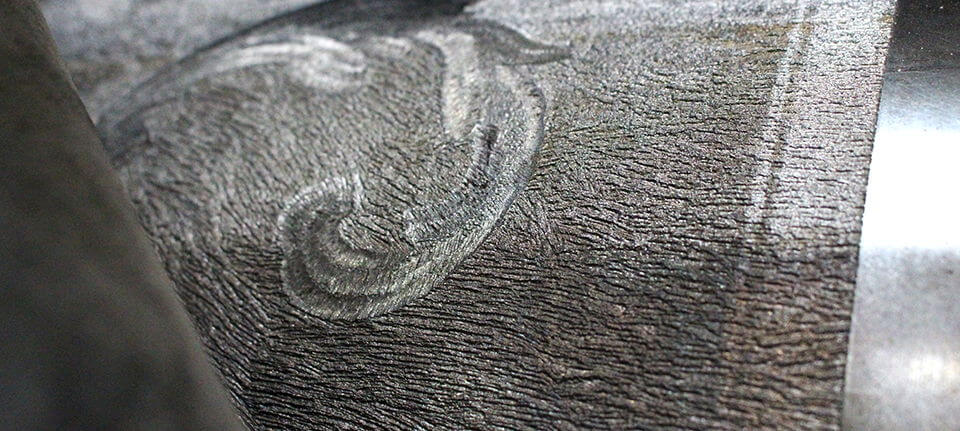
Sample realizzato da Sirpi con le più recenti tecnologie | foto di Valeria Ghion
Digital printing
Il processo produttivo di Sirpi si completa con il reparto di stampa digitale. “Abbiamo iniziato a utilizzare la stampa digitale nei primi anni del Duemila, affidandoci a fornitori esterni”, afferma Paola Jannelli. “Nel 2008 abbiamo deciso di creare un reparto digitale interno, scegliendo la tecnologia latex di HP in quanto compatibile con le normative europee in ambito di applicazioni indoor. Il parco macchine include sistemi con larghezza di 3,2 metri e 2 metri ed è in continua espansione, stiamo infatti valutando un nuovo investimento.” Inizialmente destinata alla campionatura, la tecnologia digitale – che vale circa il 30% della produzione – viene oggi utilizzata anche per produrre in piccoli e medi lotti oppure in combinazione con gli altri processi: “Stampiamo in rotocalco e goffriamo. E poi stampiamo nuovamente in digitale, per personalizzare gli articoli o creare effetti speciali. Grazie a questa tecnologia, possiamo lavorare su una vastissima gamma di supporti, dalla seta al cuoio, dalla rafia al tessuto non tessuto”. La sfida più grande del digitale? “Industrializzare il processo, per rendere il prodotto finale fruibile nelle nostre collezioni”, spiega Paola Jannelli. “Rispetto ai processi di stampa tradizionali, quello digitale ha un concept differente: non ci sono matrici, le produttività non solo elevate ed è richiesto un approccio diverso nel calcolare i margini operativi. Per industrializzarlo, abbiamo dovuto trasformare l’impronta organizzativa dei progetti.” Ed è questa la direzione anche per il futuro: “L’ambizione è quella di far crescere la produzione in digitale – meno vincolante sotto diversi punti di vista, dalla creatività alla gestione dei volumi – ma con un potenziale industriale che stiamo costruendo”.
La sostenibilità ambientale è una delle colonne portanti della strategia di Jannelli&Volpi.
“Si tratta di una vision a lungo termine, laddove le normative dell’Unione Europea sono sempre più vincolanti rispetto alle certificazioni ambientali”.
Lo stabilimento di Sirpi adotta una serie di buone pratiche per ridurre al minimo l’impatto ambientale dei processi produttivi, quali:
- utilizzo esclusivo di inchiostri a base acqua;
- circuito dell’acqua a ciclo chiuso e continuo;
- recupero dell’energia prodotta;
- utilizzo di materie prime certificate e provenienti da filiere gestite in modo sostenibile;
- controllo rigoroso delle condizioni di lavoro nello stabilimento.