Aziende di tutti i settori hanno contribuito a rispondere alla richiesta di forniture sanitarie d’emergenza, spesso lanciando e partecipando a progetti esterni al loro mercato di riferimento. Con un denominatore comune: l’utilizzo della tecnologia di stampa 3D.
La pandemia Covid-19 ha sottoposto il sistema sanitario a una pressione estremamente accentuata e, ben prima che si arrivasse a parlare di strutture ospedaliere al limite delle loro possibilità, il virus ha mandato in crisi la catena di approvvigionamento delle forniture sanitarie d’emergenza. Oggi dotarsi di mascherina è semplice, trovarla nelle prime settimane della crisi era praticamente impossibile. E quel che valeva per le mascherine, era altrettanto valido per una vasta gamma di oggetti: valvole per sistemi medicali, strumentistica, attrezzature da campo, visiere protettive, apriporta ed altri accessori di prevenzione igienica. A fronte di questa carenza, da molteplici parti c’è stata una gara di solidarietà e ingegno, per sostenere le strutture sanitarie e i loro fornitori. Una corsa che ha avuto un protagonista molto ben definito: la stampa 3D o, per usare la definizione più corretta, la manifattura additiva (AM).
Parola d’ordine: produzione
L’encomiabile riconversione e donazione alla causa da parte di operatori provenienti da ambiti altrimenti insospettabili (allestimenti e packaging per schermi separatori, meccanica e automobili per valvole polmonari, perfino makers fai da te) ha messo in luce la notevole asimmetria delle caratteristiche tecniche delle stampanti presenti sul territorio nazionale. Differenze che hanno avuto un impatto importante sulla capacità di contribuire fattivamente. Una macchina consumer con tecnologia di estrusione a filamenti di PLA o ABS (“FFF/FDM”) in una settimana di lavoro continuativo può sfornare qualche decina di pezzi, ciascuno dei quali è complessivamente fragile e qualitativamente modesto. Un sistema professional con tecnologia di fotopolimerizzazione o di stereolitografia delle resine (“MJ/PJ” o “SLA”) nello stesso periodo può produrre centinaia di pezzi, assai più curati. Sistemi con tecnologia di sinterizzazione a laser su letto di polveri plastiche (tecnologia “SLS”), infine, sono ideali per le commesse di tipo ospedaliero: possono produrre migliaia di pezzi, realizzati in materiali resistenti e stabili nel corso del tempo. Cambiano le dimensioni raggiungibili, l’accuratezza e affidabilità delle parti, tempi e quantitativi di ogni singolo lotto di produzione, investimenti necessari per il macchinario e i consumabili. E cambia la versatilità del sistema, soprattutto a fronte di piccole tirature dalle geometrie complesse a cui le tecnologie tradizionali sono meno abili a rispondere. Un valore aggiunto che corre sulla lama dell’innovazione, della reattività e della personalizzazione.
Il comparto nel suo complesso (hardware, software, consumabili e servizi) è in costante crescita e nel 2019 ha, per la prima volta, superato i 10 miliardi di dollari di valore, per uno share della manifattura globale pari al 2%. L’AM è passata dall’essere usata per applicazioni di prototipazione concettuale, appannaggio degli uffici design, a guidare lo sviluppo dell’industria, con driver di crescita quali la produzione di applicazioni funzionali da uso intermedio (tooling, posaggi, ricambi) e da uso finale (componentistica destinata al montaggio interno o al conto terzi). La disponibilità di materiali inediti, come i compositi plastici con fibra a deposizione continua (Carbonio, Kevlar) o le leghe tecniche (Inconel 625, Rame), insieme all’offerta di nuove tecnologie più semplici e accessibili che in passato – per esempio la fusione delle polveri metalliche con processo indiretto (ADAM) – alimentano la commercializzazione su vasta scala. Oltre ai settori classici (aerospaziale, automotive, gioielleria), le tecnologia di manifattura additiva stanno trovano spazio anche in altri segmenti, grazie alla loro capacità di rispondere in maniera tecnicamente adeguata e economicamente sostenibile alle criticità di processo o di prodotto di quei settori. Allo stesso modo, la presenza di nuovi materiali (biocompatibili, conduttivi, ignifughi), di nuove possibilità di miniaturizzazione o finitura apre nuovi orizzonti in segmenti tradizionalmente ricettivi quali medicale e dentale.
Storie dal fronte
Negli ultimi mesi la manifattura additiva è salita agli onori della cronaca, godendo di una popolarità solitamente sconosciuta. Una diretta conseguenza di quella gara di solidarietà e ingegno a cui facevamo riferimento prima. Narrare di tutti i protagonisti e delle loro storie non è possibile, ci limiteremo a citarne alcuni, portandoli a esempio.
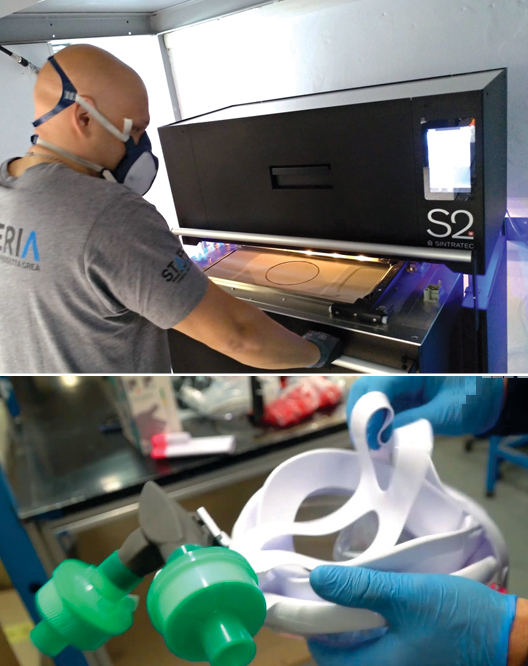
La tecnologia additiva SLS è quella più indicata per soddisfare le commesse di tipo ospedaliero. Un esempio è il modello S2 di Sintratec, il cui primo modello in Italia è stato installato da MATERIA srl con il coinvolgimento di CMF Marelli, e successivamente usato per adattare le maschere Mares.
Cominciamo da Isinnova, azienda bresciana che ha sviluppato un progetto per la trasformazione della maschere da snorkeling Decathlon in respiratori da donare ai reparti di terapia intensiva degli ospedali (immagine in apertura). Il progetto, reso disponibile gratuitamente sul sito della società, ha dato modo ad altre aziende (citiamo Ivar, bresciana anch’essa, specializzata in sistemi di riscaldamento e impiantistica sanitaria) di utilizzare i loro sistemi di AM per aumentare la produzione dei componenti necessari alla trasformazione. Un altro caso è quello che ha visto la stretta collaborazione fra MATERIA srl, service di progettazione e costruzione con sede a Rapallo, e Mares, produttore italiano delle maschere da snorkeling “SeaVuDry+”. Grazie alla collaborazione tra ingegneri e alla stampante 3D modello S2 a tecnologia SLS di Sintratec (la prima installazione italiana di questo sistema), Materia ha potuto progettare e realizzare i componenti necessari per trasformare le maschere in efficaci supporti medicali adatti alla respirazione ventilata. Il tutto con l’assistenza, il coordinamento e la mediazione di CMF Marelli, distributore italiano di Sintratec, che ha fornito gratuitamente il materiale nylon PA12 da costruzione. Perfino un brand di assoluta rinomanza internazionale come Ferrari è sceso in campo, mettendo a disposizione la sua flotta di sistemi AM per realizzare componenti per ventilatori polmonari, adattatori per maschere e altro.
Le visiere protettive sono invece al centro del progetto realizzato da Weerg e PressUP, che hanno unito le rispettive competenze e dato vita a un prodotto che ha avuto centinaia di richieste a poche ore dal lancio, intasando il call center appositamente adibito e portando le due società a fare un appello a tutto i makers d’Italia affinché contribuissero a rispondere alla domanda. I primi lotti sono stati destinati gratuitamente alla Protezione Civile. Prosilas, fra i più importanti service provider europei nell’uso dei sistemi SLS, ha invece collaborato con gli Ospedali Riuniti Torrette di Ancona per la realizzazione di flussimetri, dispositivi capaci di miscelare aria e ossigeno e necessari per il trattamento dei pazienti affetti da Covid-19. Tutta la produzione è stata realizzata con sistemi Formiga P 100 Velocis di Eos usando come materiale il PA2200.
Chiudiamo la carrellata con uno sguardo più internazionale: gli studi di sopravvivenza del Covid19 hanno evidenziato come il rame sia un materiale con il quale il virus convive molto male: il laboratorio australiano 360Biolabs, specializzato in sperimentazione clinica, ha eseguito test dai quali è emerso che entro due ore il 96% del virus muore e entro cinque ora il valore sale al 99,2%. Lo studio, realizzato per testare l’efficacia del procedimento di rivestimento in rame tramite stampa 3D ACTIVAT3D, sviluppato da SPEE3D, ha già dato il via a nuove ricerche, come quella dei filtri sostituibili in rame per respiratori eseguita dall’Università di Pittsburgh in collaborazione col produttore di sistemi di AM ExOne.
Uno sguardo al futuro
La capacità di risposta in tempi molto rapidi garantita dalla manifattura additiva rappresenta, quindi, un valore aggiunto che il progressivo ritorno alla normalità non farà certo rientrare nell’ombra. E in un mondo in cui il modello di Fabbrica 4.0 rimane una delle leve aziendali su cui basare la sfida proattiva a mercati sempre più dinamici e difficili, l’AM si è ritagliata un ruolo che può solo crescere. Produzione su richiesta o in prossimità: è questa la chiamata ineludibile e la sfida stimolante aperta dalla stampa 3D.
Questo articolo è stato realizzato con la collaborazione di Marco Marcuccio, sales manager, 3D print dept, CMF Marelli