Con tassi di crescita vertiginosi nei prossimi anni e un avanzamento tecnologico sempre più forte, la manifattura additiva (AM) ha già cominciato a cambiare le regole della produzione manifatturiera su scala industriale.
- Additive manufacturing, lo scenario
- Italia, terra d’eccellenze – Intervista a EOS
- L’importanza dell’approccio consulenziale – Intervista a CMF Marelli
- Tutta la potenza del colore – Intervista a Bompan Mimaki
- Mercato in crescita, ma serve cultura – Intervista a NTG Digital
- Nel segno della sicurezza – Intervista a Olivetti
Quando venne inventata la stereolitografia, a metà degli anni ’80 del XX secolo, probabilmente nessuno pensava che da quel brevetto si sarebbe originata una galassia tecnologica che viene oggi erroneamente riassunta nel termine stampa 3D. Né che si sarebbe ramificata in molteplici settori di mercato, da quelli più fantasiosi a quelli dove le opportunità di business sono reali. Perché se leggere che la stampa 3D costruisce le case in pochi giorni è eclatante, qualunque professionista del settore sa che si tratta del classico caso tanto fumo e niente arrosto. Le possibilità del 3D sono altre, magari meno d’appeal immediato ma dagli effetti assai più dirompenti.
Questioni di terminologia
Quando si affronta questo argomento, bisogna anzitutto risolvere la confusione terminologica. A cominciare dal fatto che con la stampa le tecnologie 3D hanno poco in comune. Il termine più corretto per parlarne, soprattutto se ci si riferisce all’ambito business, è manifattura additiva (in inglese AM, additive manufacturing). Due parole che esplicano immediatamente a cosa serve – a costruire oggetti – e come questo viene realizzato – tramite la costante aggiunta di materiale.
Un mercato in espansione
Appurato di cosa stiamo parlando, vediamo ora le sue dimensioni. A livello mondiale la manifattura additiva vale oggi circa sette miliardi di dollari. Un mercato piccolo, se raffrontato con quello della stampa in piano che vale oltre 600 miliardi. Un mercato con delle potenzialità di crescita spaventose, visto che le previsioni gli attribuiscono un valore di 100 miliardi entro il 2025 con tassi di crescita anno su anno del 15%. L’Italia contribuisce con quello che oggi è un mercato da 300 milioni di euro e interessanti possibilità di espansione (dati rielaborati da Stratego Group su fonti Sirmi, ASSO.IT).
Dalla prototipazione alla produzione
L’utilizzo classico della manifattura additiva è quello della prototipazione. Dall’automotive al medicale, dall’aerospaziale alla difesa, sono tanti i settori in cui si è ritagliata il suo spazio per questo scopo. L’avanzamento tecnologico degli ultimi anni, tuttavia, ha avviato un processo di forte cambiamento, rendendo la manifattura additiva pienamente utilizzabile in ambito produttivo a livello industriale. Le macchine hanno raggiunto alti livelli di produttività con una qualità finale altrettanto elevata, con tempi di lavorazione decisamente accorciati e una maggior fluidità dei processi. Se prima usavano la manifattura additiva unicamente per vedere una bozza del progetto, oggi le industrie la scelgono per realizzare quello stesso progetto in maniera innovativa, con risultati paragonabili se non addirittura superiori ai metodi tradizionali, e con una possibilità di personalizzazione prima sconosciuta. I progettisti dell’automotive si ritrovano per le mani uno strumento che garantisce loro una libertà di design che i tradizionali metodi di tipo sottrattivo non consentono. Nell’aerospaziale molti componenti possono essere realizzati con significativi mutamenti nelle caratteristiche del pezzo stesso – quali l’accrescimento della resistenza e la diminuzione del peso. Il medicale fa della personalizzazione un aspetto fondamentale, potendo creare protesi che siano perfettamente adattabili a uno specifico paziente. Non è un caso che nei prossimi anni il tasso di crescita delle macchine additive in questi ambiti sia, rispettivamente, del 34%, del 26% e del 23% (dati Frost&Sullivan). Al contempo, altri settori di business si vanno aprendo alla manifattura additiva: gioielleria, allestimenti, comunicazione e molti altri.
Materiali
Una tematica molto importante nell’ambito additivo è rappresentata dai materiali. Plastici e metallici sono i due principali raggruppamenti, ma esistono tecnologie che funzionano anche con composti, cera, gel, sabbia e perfino carta. Questo perché l’offerta è estremamente variegata e le differenze tra una tecnologia e un’altra sono piuttosto elevate. Inoltre, affermare di utilizzare un materiale di un certo tipo è estremamente riduttivo, in quanto per ciascuna macrocategoria sul mercato ne esistono decine e decine. I produttori di tecnologie sono spesso anche produttori dei materiali di consumo, ma esistono tanti altri attori che si sono specializzati unicamente nella produzione e fornitura dei consumabili. Senza contare enti quali i poli universitari, i cui programmi di ricerca e consulenza spesso conducono alla realizzazione di nuovi materiali specifici per determinate applicazioni.
Software
Qualunque sistema tecnologico di un certo livello è gestito da un programma software dedicato. Questo vale anche per la manifattura additiva che però, soprattutto nei sistemi di fascia alta, abbraccia sempre più i concetti di produzione connessa, di integrazione tecnologica e di automazione intelligente che sono alla base dell’Industry 4.0 e di tutti i suoi vantaggi. In questo ambito, i software giocano un ruolo fondamentale, gestendo tutto il processo produttivo – dalla progettazione CAD alla lavorazione in macchina alle fasi di finitura del prodotto e alla sua logistica di consegna – andando a formare architetture informatiche tramite le quali si possono controllare tutte le operazioni, ottenere dati puntuali e in real-time sull’andamento della produzione, calcolare l’attuale efficienza dei processi e ideare strategie per migliorare l’intero sistema aziendale.
Sguardo al futuro
Benché l’offerta tecnologica sia ormai molto sviluppata e sia possibile costruire flussi di lavoro anche molto complessi, resta ancora molto da fare prima che la manifattura additiva si diffonda nell’industria in una misura tale da poter, se non mutarne completamente i metodi produttivi, quantomeno esserne parte integrante su vasta scala. Prima ancora che un ulteriore scatto tecnologico, la criticità risiede nella capacità delle aziende di guardare al futuro e crearsi le competenze necessarie a integrare la manifattura additiva nei propri processi. Sondando il mercato emerge come da molte parti non ci sia quella volontà di rischiare, preferendo attendere che qualcun altro faccia il primo passo e mostri la strada, per poi entrare in un mercato con delle regole già stabilite. Tuttavia ci sono aziende dotate di spirito pionieristico, che sono nate seguendo intuizioni quasi da sognatori e hanno alle spalle una storia tutt’altro che semplice; costoro oggi stanno raccogliendo i frutti del loro rischio e mostrando a tutti che fare da apripista è stata una scelta magari azzardata ma che alla fine ripaga con tutti gli interessi del caso. Sono aziende che, in Italia come in tanti altri luoghi del mondo, si stanno ritagliando uno spazio importante nel mercato e sfruttano appieno il vantaggio competitivo che hanno acquisito per diventare partner primari sia dei grandi gruppi con respiro internazionale (basti pensare ai settori dell’automotive o dell’aerospaziale) che di tante realtà che formano il tessuto industriale del nostro Paese e che, pur non avendo le competenze interne, hanno comunque saputo cogliere i benefici rappresentati dalla manifattura additiva per il loro business.
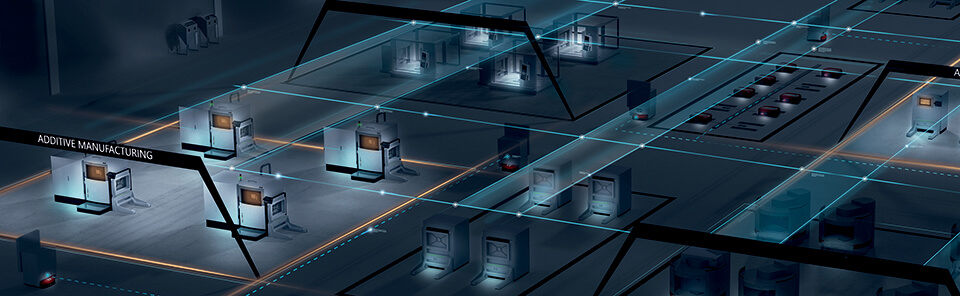
Schema di un sito produttivo AM smart e interconnesso. (fonte: EOS)
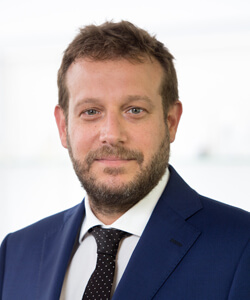
Giancarlo Scianatico, regional manager EOS per l’Italia
Fondata nel 1989 e con sede in Germania, EOS è un fornitore globale di soluzioni complete di manifattura additiva. Il suo portfolio di prodotti comprende soluzioni per la manifattura in metallo o a polimeri, software gestionali e materiali di consumo. Tra i principali settori industriali a cui si rivolge ci sono: l’aerospaziale (parti di motori, turbine, componenti interni dei velivoli); l’automotive (componenti di alta qualità ingegneristica e a elevata personalizzazione); il medicale (strumenti chirurgici e dispositivi medici specializzati per odontoiatria, ortopedia e implantologia con livelli di personalizzazione totali). Abbiamo chiesto a Giancarlo Scianatico, regional manager per l’Italia, un quadro del mercato nazionale.
La stampa additiva sta completando il passaggio dalla prototipazione alla produzione industriale di parti finite. Quanto è pronto il mercato italiano per questo passo?
Da sempre il mondo dell’innovazione è un ambiente che attrae gli imprenditori e i professionisti italiani e l’additive manufacturing non si sottrae a questa tendenza. A tal punto che negli ultimi due anni abbiamo potuto notare un incremento esponenziale dell’interesse dimostrato da parte delle aziende italiane nei confronti di una tecnologia dalle straordinarie potenzialità. Le novità, però, hanno spesso bisogno di un periodo di assestamento, soprattutto per la reale comprensione delle loro caratteristiche e possibilità. Per questo motivo, ancora oggi vediamo che ci sono realtà industriali nel nostro Paese che continuano a non comprendere a pieno di cosa si stia parlando quando si nomina la manifattura additiva industriale. Siamo tuttavia convinti che in Italia ci siano ottime opportunità di crescita e sviluppo sia in termini di nuove generazioni di professionisti del settore, sia di nuovi progetti in grado di scommettere davvero sull’innovazione proposta dalla quarta rivoluzione industriale.
Qualche esempio d’eccellenza nel nostro Paese?
Fra i clienti italiani con cui nell’arco degli anni abbiamo potuto costruire una collaborazione costante e proficua, possiamo citare Prosilas, azienda nata nel 2003 e specializzatasi nella tecnologia SLS fino a diventare partner di grandi gruppi industriali sia per la prototipazione che per la produzione in serie di componenti; e il Politecnico di Torino, che fin dagli anni ’90 porta avanti una serie di progetti legati alla manifattura additiva che sono sfociati in pubblicazioni scientifiche, collaborazioni consulenziali per aziende, la creazione di un centro di ricerca interno e la formazione di un master di II livello dedicato. Sono entrambe realtà che si pongono come eccellenze ed esempi di un tessuto imprenditoriale e formativo in grado di fare rete e di porre le basi per un nuovo percorso della produzione additiva che punti dritto verso quell’Industry 4.0 di cui tutti parlano e per cui le nostre soluzioni sono pronte.
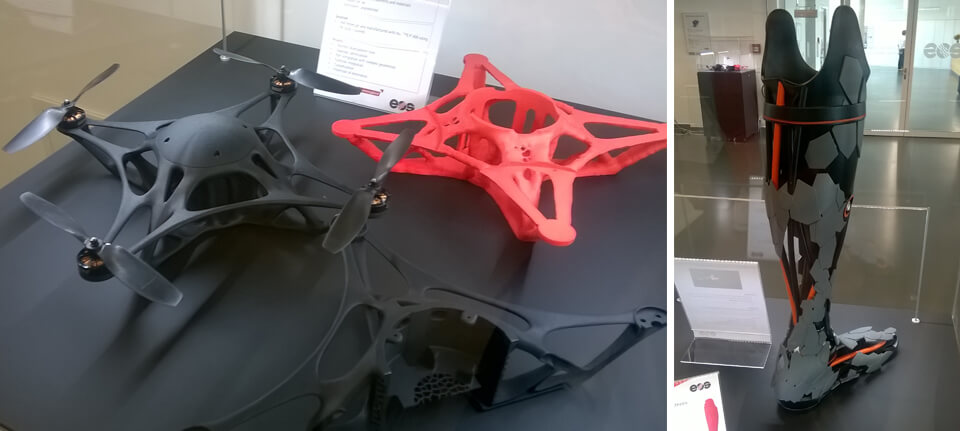
Esempi applicativi realizzati con macchine EOS: parti per droni e, a destra, una protesi ad alta personalizzazione.
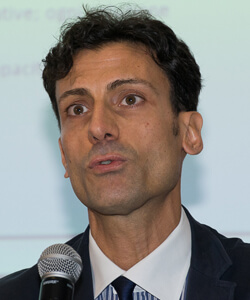
Marco Marcuccio, sales manager di CMF Marelli
Precursore dell’additive manufacturing in Italia e fra i primi operatori a livello europeo, CMF Marelli è rivenditore dei sistemi a marchio Markforged per materiali compositi e metallici; delle soluzioni in materiali fondibili Solidscape; e di altri marchi per specifiche nicchie professionali. Abbiamo parlato del ruolo del rivenditore con Marco Marcuccio, sales manager di CMF Marelli.
Nel contesto attuale del mercato, in costante espansione e con nuove nicchie che nascono ogni giorno, come si declina il ruolo del rivenditore?
Il tipo di approccio e di competenze necessarie si diversifica molto a seconda della tecnologia e delle applicazioni. Nell’ambito professionale/industriale, le aziende sono interessate a fare investimenti che siano il più possibile adeguati alle loro specifiche esigenze. Di conseguenza, il nostro compito in qualità di rivenditori è di assistere il potenziale cliente nella sua indagine di adeguatezza tecnica e sostenibilità economica, per poi accompagnarlo nel percorso di ottimale utilizzo dei materiali, di aggiornamento dei software e di corretta manutenzione dell’hardware. Avere una capacità consulenziale a tutto tondo è la vera discriminante del successo di una trattativa.
Quali sono i rapporti con le case madri, in particolare in relazione ai feedback ricevuti dai clienti e che possono essere utili ai reparti di R&D?
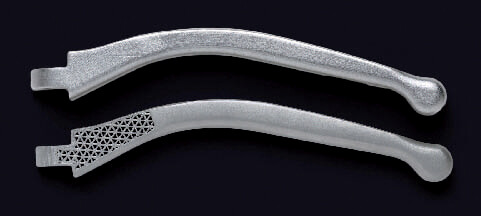
Parti realizzate con il sistema Metal X di Markforged, distribuito in Italia da CMF Marelli.
I nostri rapporti con le case madri sono di intensa e costante collaborazione, soprattutto riguardo gli aspetti di applicazione ingegneristica e di resa commerciale sul canale. Considerando che – per definizione – i brand di manifattura additiva sono compagnie a fortissima concentrazione tecnologica, i loro programmi di R&D si articolano in progetti complessi e lunghe pianificazioni che di solito possono essere influenzati solo marginalmente da specifiche esigenze provenienti dai singoli mercati. Ciò non toglie che il rivenditore, che agisce più strettamente sul territorio, riporti alla casa madre specifiche richieste emerse dai suoi rapporti coi clienti e che possono risultare interessanti. Va comunque sottolineato che in molti casi determinate esigenze di singoli clienti vengono trattate direttamente a livello locale focalizzandosi sulla soluzione già esistente che più si avvicina alle necessità del singolo.

Rachele Bompan, ceo Bompan
Multinazionale con una lunga storia di successo nella stampa 2D, Mimaki è recentemente entrata nel mondo della manifattura additiva con una soluzione proprietaria, Mimaki 3DUJ-553. Ne abbiamo parlato con Rachele Bompan, ceo dell’importatore esclusivo per l’Italia Bompan.
Quali sono le caratteristiche dell’offerta tecnologica Mimaki? A quali settori si rivolge?
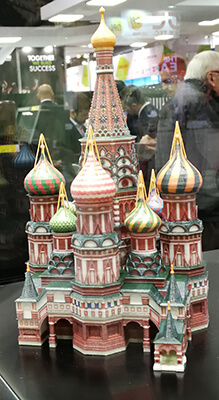
Un esempio che mostra il livello di dettaglio e le possibilità cromatiche ottenibili col sistema Mimaki.
Mimaki 3DUJ-553 è un sistema con delle particolarità di assoluto rilievo. Prima fra tutti quella di poter riprodurre direttamente oltre 10 milioni di colori in strati sottilissimi, fino a un minimo di 19 micron, restituendo lavori in qualità fotografica. La disponibilità di inchiostro clear permette, inoltre, di creare oggetti con trasparenze o semitrasparenze per effetti ancora più ricercati. La lavorazione utilizza un materiale di supporto idrosolubile, che può essere facilmente lavato via; questo elimina la necessità di operazioni manuali e riduce drasticamente la possibilità di danneggiare il prodotto durante la rimozione. L’area di produzione, pari a 50x50x30 cm, permette di realizzare pezzi di notevoli dimensioni con design estremamente complessi e dettagliati. Queste caratteristiche ampliano esponenzialmente i possibili mercati di riferimento: dal mondo della comunicazione visiva fino agli allestimenti per punti vendita, dalla prototipazione all’architettura, passando per il fashion e il medicale.
Quale interesse avete riscontrato finora? Quali sono gli obiettivi che vi siete posti, anche in riferimento al mercato italiano?
Fin dalla presentazione ufficiale abbiamo registrato riscontri estremamente positivi e un interesse crescente in tutti gli appuntamenti a cui abbiamo partecipato – da FESPA Berlino a maggio fino al recente Viscom Italia. Mimaki 3DUJ-553 ha anche ricevuto due riconoscimenti significativi: è stata selezionata come innovazione dell’anno ai 3DPI Awards 2018 ed è stata insignita del prestigioso premio EDP 2018 come migliore stampante 3D additiva full-color. Due premi che riflettono la componente rivoluzionaria di questo sistema, capace di infiniti ambiti applicativi. Forti di un prodotto così innovativo, siamo certi di poter replicare anche in ambito additivo il percorso già realizzato con la stampa in piano, sfruttando la sinergia tra Mimaki e Bompan per approcciare i clienti in maniera totalmente trasversale, indipendentemente dal loro mercato verticale di appartenenza.
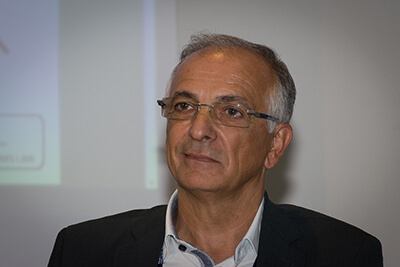
Ignazio Binetti, sales and marketing manager NTG Digital
NTG Digital è distributore dal 2016 di Massivit 3D, azienda israeliana che ha sviluppato una soluzione di manifattura additiva in grado di produrre parti o pezzi finiti di grandi dimensioni. Utilizza la tecnologia proprietaria GDP (Gel Dispensing Printing) che sfrutta Dimengel, un gel plastico monocromatico che può essere liberamente rifinito con varie lavorazioni di finishing. I suoi mercati di riferimento sono quelli della comunicazione e degli allestimenti. Ne abbiamo discusso con Ignazio Binetti, direttore marketing & vendite di NTG Digital.
Qual è il mercato potenziale a cui vi rivolgete in termini di operatori e copertura del territorio? Che risposta state ottenendo?
La tecnologia Massivit 3D rappresenta un’alternativa ai metodi tradizionalmente usati per la realizzazione di lavorazioni tridimensionali per allestimenti teatrali, eventi, pubblicità e punto vendita. Questi ultimi, tuttavia, risultano o più complessi (come la termoformatura) o di qualità decisamente inferiore (come il polistirolo). Questo offre un mercato di riferimento piuttosto ampio e in crescita, anche se lentamente, grazie a quelle aziende dotate di spirito pionieristico – come le quattro installazioni Massivit 3D in produzione presenti sul territorio nazionale – che scelgono di indicare la via a tutti gli altri.
Nel dialogare con gli stampatori, quali sono le principali criticità che vi trovate ad affrontare?
Gli stand Massivit agli appuntamenti fieristici suscitano sempre molto interesse, che però in molti casi si affievolisce nel momento in cui lo stampatore incontra difficoltà nel comprendere le reali potenzialità della manifattura additiva per il suo business. La mancanza di cultura generale sull’argomento spesso risulta essere un ostacolo anche per coloro che hanno investito in soluzioni additive e devono far capire ai loro clienti i vantaggi rispetto alle tradizionali soluzioni sottrattive – parliamo ad esempio di una visibilità cinque volte superiore rispetto alla comunicazione 2D. Il nostro lavoro, pertanto, è fortemente orientato alla consulenza e alla formazione culturale. I corsi che proponiamo si focalizzano anche su due criticità di grande importanza per coloro che hanno deciso di dotarsi di una soluzione additiva: la gestione del file e la finitura del prodotto. Nella stragrande maggioranza dei casi il cliente non possiede un file pronto, ma un’idea astratta da cui partire per creare il modello tridimensionale da inviare successivamente in macchina. Il prodotto che ne esce non è però finito: il gel proprietario Massivit 3D, infatti, è un materiale monocromatico che può essere rifinito in molteplici modi – ad esempio, tramite verniciatura e levigazione. Simili aspetti legati al flusso di lavoro possono risultare ostici per chi si sta affacciando a questi mercati, dato che spesso non possiede ancora le competenze interne per gestirli adeguatamente. Il nostro ruolo deve essere anche quello di fornire modi per acquisirle.
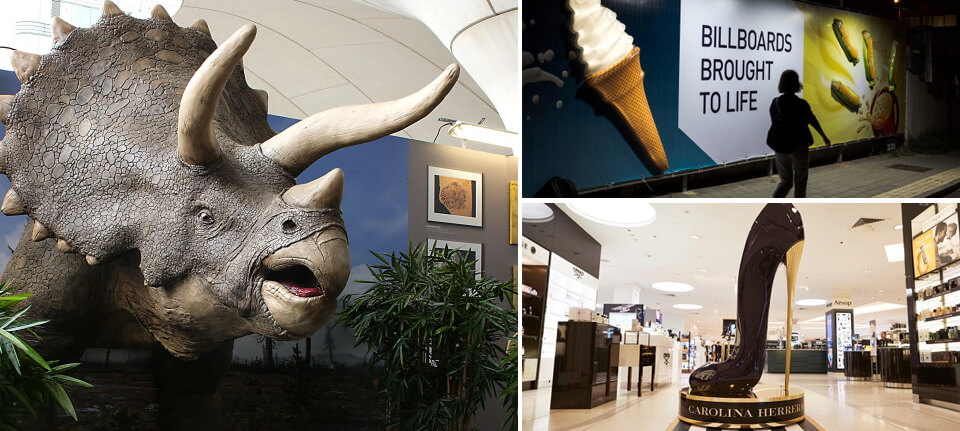
Sono molteplici le possibilità applicative dei sistemi Massivit 3D: dall’allestimento del punto vendita alla pubblicità di mostre, fino alla commistione con la stampa 2D per cartellonistica outdoor.
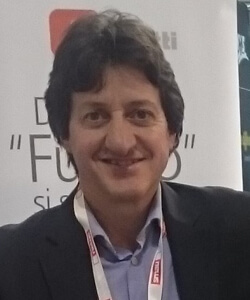
Jacopo D’Auria, 3D printing business development Olivetti
Nel campo della manifattura additiva Olivetti vanta un’offerta articolata in tre modelli, tutti con tecnologia FDM/FFF (Fused Deposition Modeling), che si rivolgono ad ambiti differenti, dal manifatturiero/industriale allo scolastico/formativo. Ponendo delle criticità legate alla sicurezza e al rispetto delle normative. Ne abbiamo discusso con Jacopo D’Auria, 3D printing business development di Olivetti.
La presenza di soluzioni ibride nell’ambito della manifattura additiva è ormai un dato di fatto. Qual è la situazione normativa al riguardo?
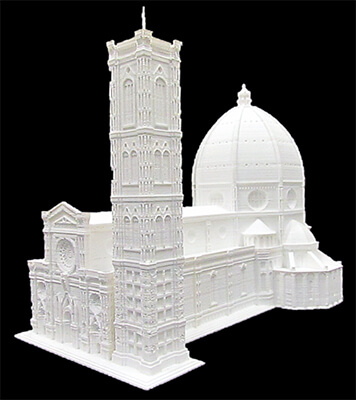
Modellino tridimensionale della cattedrale di Santa Maria del Fiore a Firenze, realizzato con sistemi Olivetti.
C’è ancora bisogno che venga posta una piena attenzione sui temi riguardanti le condizioni e le modalità di impiego dei sistemi di manifattura additiva in ambienti nei quali hanno grande rilevanza gli aspetti di sicurezza: parliamo di ambiti produttivi/industriali, ma anche di quelli scolastici. Questo perché esistono soluzioni – e l’offerta di Olivetti rientra tra queste – che sono progettate per adattarsi a una molteplicità di ambienti le cui regole possono essere diverse. In particolare per le soluzioni desktop è ancora poco definita l’applicazione delle normative riguardanti la sicurezza degli operatori nelle varie fasi del “ciclo di vita” delle macchine.
Come risponde Olivetti?
Nella progettazione dei nostri sistemi abbiamo fatto della sicurezza un aspetto fondamentale. La soluzione S2 di grande formato, il cui target specifico è il settore manifatturiero e industriale, è pienamente conforme alle direttive internazionali EMC, MD e ROHS. Inoltre, ha superato tutti i test previsti per la Certificazione di Sicurezza per i Macchinari ad uso industriale (Direttiva Macchine – 2006/42/CE) e altri test atti a garantire un’ottimale resistenza a stress meccanici e ambientali, risultando pertanto equiparata per sicurezza a un sistema di lavorazione manifatturiera tradizionale. Per quanto riguarda 3D Desk, la nostra offerta per l’ambito scolastico e formativo, alla conformità alle direttive si va ad aggiungere un’attenzione particolare dovuta proprio all’ambiente a cui il sistema è destinato. A differenza di molte altre stampanti di tipo desktop, 3D Desk ha una struttura a chiusura ermetica con serratura di sicurezza per garantire la massima tutela dell’incolumità di insegnati e studenti. Anche grazie a questo siamo stati scelti come partner del progetto “Kit Scuola 3D”, lanciato dalla Regione Lazio, nell’ambito del quale abbiamo fornito macchine a oltre duecento istituti scolastici.