In questo articolo analizzeremo la stampa su legno. Lo faremo, certo, ma scrivendolo ci siamo accorti che quando si parla di legno in realtà si intendono spesso suoi derivati. E quando si parla di stampa su legno, non si intende tanto stampa decorativa, quanto imitativa del legno su carta. Sembra complesso? Seguici in questo viaggio, e tutto sarà più chiaro.
Il legno è un materiale organico, proprio come la pelle, di cui abbiamo parlato su WIDE 42. Viene usato in modo massiccio nel settore dell’arredamento e dell’edilizia, ma trova impiego in numerosi settori, dagli strumenti musicali ai giocattoli. Come al solito, partiremo da molte domande, e cercheremo di dare qualche risposta:
- Quando si stampa su legno?
- Qual è la destinazione d’uso del prodotto finito?
- Che resistenze sono necessarie, durante la lavorazione e dopo?
- Quali lavorazioni sono necessarie per arrivare al prodotto finito?
- Ho bisogno di pretrattamento e post-trattamento?
- Quale tecnica di stampa userò?
- Quale inchiostro?
Cominciamo però dalla base. “Per fare un tavolo ci vuole il legno. Per fare il legno ci vuole l’albero”, cantava Sergio Endrigo. Tutto parte da qui, infatti: dagli alberi. Il legno serve alle piante a portare in alto, alla luce, le parti verdi in cui avviene la funzione clorofilliana. In questo articolo ci riferiremo sempre alle piante dicotiledoni; escluderemo cioè palme, bambù e altre specie, il cui tessuto di sostegno si chiama “stipite”. Per l’arredamento e l’edilizia viene usato il fusto dell’albero. La chioma viene usata come legna da ardere. Nel tronco degli alberi si identificano due macro sezioni: quella esterna si chiama zona corticale, ed è composta da corteccia, libro e cambio. Quella interna è il legno propriamente detto, ed è composta da alburno, durame e midollo. La corteccia viene eliminata in sede di lavorazione. Il libro è uno strato formato da condotti nei quali discende la linfa. Il cambio è un sottile strato tra corteccia e legno, che produce nuove cellule che determinano l’accrescimento del fusto in senso radiale. La parte più interna è formata dall’alburno e dal durame, sezioni che possono essere distinguibili o meno tra loro. Li si riconosce perché nei climi temperati la successione delle stagioni determina i cosiddetti “anelli di accrescimento”, gli elementi che poi formano le venature. Il cuore del tronco si chiama midollo. È poco compatto, ha una consistenza minore rispetto ad alburno e durame, e ha un aspetto spugnoso: questa struttura è finalizzata all’accrescimento assiale del fusto.
Fisica e meccanica del legno: cosa serve sapere prima di stampare
Dal punto di vista fisico, il legno è un materiale poroso: circa il 50-60% del suo volume è costituito da cavità. Sono i capillari, che finché l’albero è vivo trasportano la linfa. Questa particolare conformazione del tronco, interamente percorso da capillari, è il motivo principale della cosiddetta igroscopicità del legno. Tale materiale, infatti, assorbe acqua dall’aria e la trattiene in forma liquida, nei pori oppure nella parete cellulare. La sua struttura porosa può essere sfruttata anche per impregnarlo di liquidi protettivi, coloranti o adesivi. Quando si parla di stampa diretta su legno, bisogna tenere conto di questa caratteristica. Infatti, se non si prevede un pretrattamento che chiuda i pori in superficie la quantità di inchiostro necessaria sarà molto maggiore. L’umidità del legno ne influenza tutte le caratteristiche fisiche, meccaniche e tecnologiche: dall’elasticità alla sua tendenza anisotropa al ritiro e rigonfiamento lineari e volumetrici. La stabilità dimensionale del legno è un aspetto fondamentale da considerare, anche quando si parla di stampa. Può essere garantita se in fase di lavorazione il legno ha un’umidità che si manterrà in equilibrio con le condizioni ambientali anche nel successivo impiego. Non esiste una “umidità perfetta” del legno, ottimale e costante in ogni caso. Con un’umidità inferiore al 20% i fenomeni di degrado fungino più noti e frequenti non si innescano. Sopra al 20% le sue caratteristiche meccaniche si riducono, benché non in modo drastico. Se non entra direttamente in contatto con l’acqua, l’umidità del legno resta al di sotto del 20%, a meno di avere condizioni di umidità relativa dell’aria prossime al 100%. In ambiente normale, l’umidità del legno varia fra il 10 e il 20%. Se si vogliono evitare gli effetti collaterali della variazione di umidità, occorre mantenere condizioni climatiche costanti, ma questo è difficile anche nelle abitazioni private, dove a seconda della stagione l’umidità varia di 6-8 punti percentuali. La soluzione migliore è cercare di tenere il manufatto in equilibrio col clima (temperatura e umidità relativa) in cui è in servizio, valutando la situazione caso per caso. Tradizionalmente i legni vengono classificati in base alla loro durezza. Da questa dipendono spesso anche le loro destinazioni d’uso. I legni si differenziano anche per il loro aspetto: dal colore (bruno, rossastro, nero) al disegno, che dipende dal taglio e dall’andamento delle fibre (lucentezza, grana, venatura).
![]() |
Abete | Facilmente lavorabile, esiste in due varietà: bianco o rosso | Cellulosa, costruzioni, infissi, mobili, scale, pavimenti, facciate, balconi, rivestimenti di pareti e soffitti, mobili, imballaggi, cassette, strumenti musicali |
![]() |
Betulla | Leggero e pieghevole | Carta, costruzioni, compensati, impiallacciature di pregio, parquet, mobili colorati, oggetti torniti, giocattoli, utensili da cucina, segati, sculture, pannelli di fibre e trucioli, legna per caminetti |
![]() |
Larice | Pregiato, elastico e durevole | Barche, infissi, scale, pavimenti, strutture portanti e non, elementi costruttivi molto sollecitati, ponti, parti interrate e immerse in acqua, mobili |
![]() |
Pino | Resinoso, resistente e durevole | Barche, pali, ponti, scatole, matite, interni, mobili, pannelli, parti costruttive incollate, parchi giochi, pali, combustibile cippato, brikett e pellet |
![]() |
Pioppo | Poco resistente ma lavorabile facilmente | Carta, casse da imballaggio, compensati, fiammiferi, mobili, cellulosa, pannelli truciolari, impiallacci pregiati |
![]() |
Faggio | Fibre compatte, si presta bene all’incurvamento | Barche, mobili, pavimenti, sedie, impiallacciature e compensati, scale e parquet, giocattoli, utensili da cucina, spazzole e parti di attrezzi, cassette per la frutta, traversine ferroviarie, cellulosa, pannelli in materiale legnoso, legna da ardere, carbone |
![]() |
Frassino | Robusto e flessibile | Stecche da biliardo, mobili, pavimenti, scale, mobili in legno piegato, attrezzature sportive, attrezzi da lavoro, strumenti musicali |
![]() |
Noce | Resistente, facilmente lavorabile, apprezzato per le venature | Intarsi, mobili, interni, impiallacciature, tornitura, strumenti musicali, calci di fucile |
![]() |
Quercia | Duro, resistente ed elastico; ne esistono diverse qualità: rovere, leccio,… | Barche, botti, travi, traversine ferroviarie, impiallacciature per mobili, serramenti, scale, rivestimenti soprattutto per esterni |
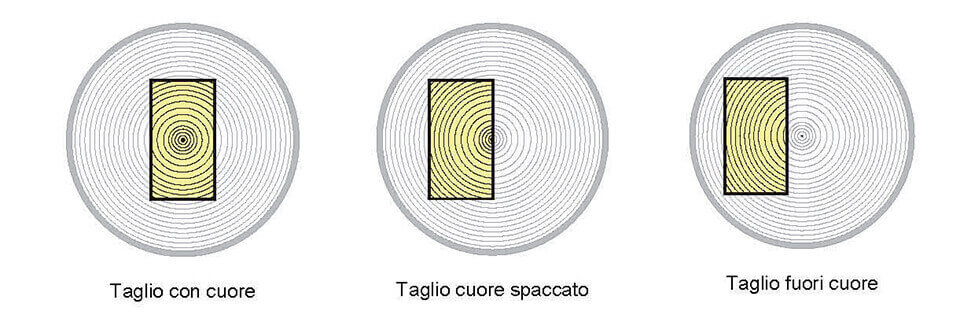
Tre tipi di tagli possibili. Nel primo caso si avranno stabilità dimensionale e rischio di fessurazione molto alti, nel secondo saranno alti, nell’ultimo invece saranno limitati. fonte immagine: Promo Legno
Legno massiccio: pro e contro
Il legno nasce cilindrico: questa è infatti la forma del tronco. In alcuni casi viene impiegato nella sua interezza, come legno massiccio. In questo caso il tronco viene tagliato in modo da mantenere una sezione rotonda, oppure – più spesso – rettangolare. Quest’ultima forma è generalmente più duttile e pratica, sia per le successive lavorazioni che per la conservazione e lo stoccaggio. Il legno viene suddiviso sulla base del taglio: se è centrale si chiama taglio con cuore; se un lato è tangenziale alla linea di diametro del tronco si chiama taglio cuore spaccato; se non include il cuore si chiama taglio fuori cuore. Dal tipo di taglio dipendono stabilità dimensionale (deformazioni e svergolamento) e rischio di fessurazione della tavola o della trave: nel primo caso sono molto alti, nel secondo sono alti, nel terzo sono limitati. Per aumentarne dimensione e resistenza, soprattutto se usati in ambito strutturale, vengono incollate due o più porzioni di massello. A seconda delle dimensioni, si chiamano listello, tavola, tavolone o legname squadrato. Il problema del legno massiccio è però il suo costo. La resa di un tronco infatti è solamente del 15-20%.
Del legno non si butta via niente: derivati e compositi da piallacci, fibre e trucioli
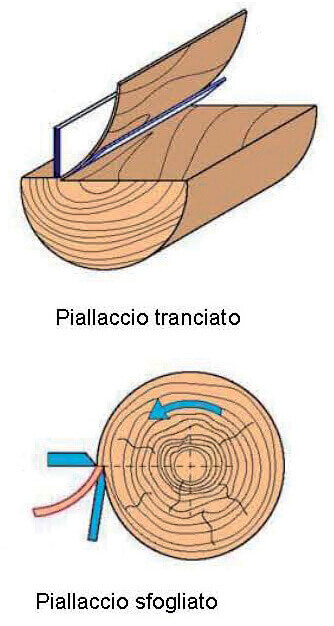
I due modi in cui vengono ottenuti i piallacci: per tranciatura o per sfogliatura
Ma il legno – perdonateci il paragone – è un po’ come il maiale, non si butta via niente. Ecco quindi che molto spesso i tronchi o le parti di scarto vengono tagliati e poi ricomposti in vari modi. I materiali di partenza possono essere piallacci, trucioli o fibre di legno. Vengono lavorati e ricomposti, usando colle speciali, così da essere utilizzabili. Anche in questo caso vengono realizzati prodotti lineari oppure piani, come i pannelli truciolari, OSB e in fibra di legno.
I pannelli da piallacci
Il tronco può essere tranciato o sfogliato, in modo da ottenere fogli più o meno sottili, detti rispettivamente “piallacci” o “sfogliati”. La sfogliatura è un processo semplice ed economico, e quindi più adatto alle produzioni di massa. Richiede però materiale con elevate caratteristiche geometriche, ovvero un buon diametro e una buona rettilineità dei tronchi. Il taglio a strati è invece adatto a lavorazioni più pregiate, come l’impiallacciatura. In questo modo si riesce anche a mantenere la fiammatura del legno, il disegno. I piallacci ottenuti tramite sfogliatura o tranciatura vengono essiccati, levigati, selezionati ulteriormente e tagliati nel formato desiderato. Dai piallacci vengono composti prodotti lineari, detti “stratificati di piallacci”, e prodotti piani, come i compensati.
I pannelli da fibre di legno
I fasci di fibre vengono ottenuti con un processo di sfibratura, dopo che il legno grezzo è stato sottoposto a una prima riduzione in minuzzolo. Le fibre si legano nel pannello intrecciandosi tra loro e sfruttando l’azione adesiva del legno stesso. È possibile anche aggiungere altre sostanze adesive alla miscela. In base come vengono prodotti, i pannelli di fibra di legno vengono suddivisi in “pannelli per via umida” e “pannelli per via secca“.
I pannelli da trucioli
I pannelli truciolari possono essere classificati in base alla struttura del pannello, ovvero monostrato, multistrato (composti da particelle orientate o non orientate all’interno di ciascuno strato), a separazione progressiva simmetrica, pannelli estrusi con tubi. Possono essere classificati anche in base alle dimensioni e alla forma delle particelle: pannelli di trucioli sminuzzati (pannelli truciolari), pannelli di trucioli grossi e ampi (waferboard), pannelli di trucioli lunghi, stretti e orientati (OSB), pannelli di altri materiali.
FIBRE
Pannelli in fibra di legno porosi: pannelli impiegati soprattutto nell’isolamento termico e acustico. Il legno viene ridotto in fibra nello sfibratore, steso su un primo percorso di essiccazione e – se serve – miscelato con additivi. Viene precompattato e infine passato in un essiccatoio a rulli.
Pannelli in fibra di legno duri e medio-duri: a differenza dei pannelli di fibra porosi vengono pressati ad alta temperatura. I processi produttivi avvengono per via umida. I trucioli vengono disintegrati tramite saturazione con vapore acqueo; la pressione viene ulteriormente innalzata e infine le fibre vengono spruzzate o spalmate su uno schermo a pressione atmosferica. È la lignina a legare le fibre, quindi non sempre servono ulteriori adesivi. Alcuni di questi materiali sono noti per i loro nomi commerciali: tra questi masonite, faesite, isorel, hernit, karlit, torex e treetex.
Pannelli di fibra di legno a media densità o MDF: pannelli realizzati per via secca. Le fibre di legno, mescolate con colle molto resistenti ed essiccate, vengono compattate in presse continue. A differenza del truciolare, può essere lavorato come se fosse legno massiccio senza che si sbricioli, cioè intagliato e fresato. Presenta una superficie estremamente liscia e compatta, e viene quindi verniciato, dipinto o stampato facilmente. Viene usato soprattutto nell’arredamento.
TRUCIOLI
Pannelli piani pressati incollati con resine sintetiche o truciolari: sono composti da legno massiccio (principalmente di scarso valore, piccolo e fragile), trucioli (di segatura, di pialla) e legno riciclato o vecchio. I pezzi vengono sminuzzati in modo meccanico. Vengono suddivisi in frazioni granulometriche, che sono miscelate in maniera omogenea e servono a comporre gli strati interni ed esterni. I trucioli vengono essiccati, controllati e incollati con agenti leganti. I più comuni sono resine ureiche, melamminiche e fenoliche. Esistono però anche pannelli legati con cemento, gesso e la stessa lignina che è contenuta nelle fibre del legno. Vengono quindi incollati in superfici piane, orientati in direzione parallela alla superficie stessa. A questo punto questo “materasso di trucioli” viene pressato, raffreddato, rifilato, levigato e tagliato.
OSB (Oriented Strand Board): pannelli per lo più a tre strati composti da trucioli piatti (strand in inglese). I trucioli degli strati esterni, geometricamente simili, sono orientati parallelamente alla direzione di produzione. I trucioli dello strato interno vengono invece orientati a caso o perpendicolarmente alla direzione di produzione. Lo strato interno ha una densità minore, perché contiene più materiale fine e materiali con maggiore variabilità geometrica e dimensionale.
PIALLACCI
Compensato: plywood in inglese, è un pannello creato componendo fogli di piallaccio con fibre giustapposte. Sono incollati con adesivi durevoli e resistenti all’umidità, in presenza di pressione e calore. Alternando la direzione delle fibre dei diversi strati, la rigidità e la resistenza del pannello di compensato sono massimizzate in entrambe le direzioni. Legno stratificato: materiale composto da fogli di piallaccio con fibre parallele tra loro. Non si differenzia molto da prodotti lineari, come massello o lamellare, caratterizzati da una resistenza monodimensionale.
TAVOLE E LAMELLE
Pannelli di legno massiccio monostrato e multistrato: pannelli composti da tavole o lamelle di uguale spessore, incollate tra loro. Sono “monostrato” se i diversi elementi di legno che li compongono formano un unico strato, e “multistrato” se hanno due strati esterni con fibre orientate nella stessa direzione e almeno uno strato interno con fibre orientate perpendicolarmente.
Legno lamellare: travi solide e resistenti usate in ambito strutturale; riducono i difetti del legno massiccio. Vengono prodotte incollando a freddo e sotto pressione lamelle parallele fra loro, impilate e incollate una sull’altra. Possono arrivare a una lunghezza di oltre 40 metri.
Legno compensato di tavole: materiale solido e resistente che riduce i difetti del legno massiccio. Usato in ambito strutturale, viene prodotto incollando a freddo e sotto pressione lamelle o tavole che formano pannelli di legno multistrato stabilizzati dal punto di vista igrometrico. Come nel compensato, questi pannelli vengono posizionati con venatura in direzione ortogonale tra loro, in modo da garantire una resistenza più uniforme.
MISTI
Panforte: pannelli composti da due strati esterni di compensato e uno strato interno di listelli di legno massiccio.
Pretrattamento, stampa, post-trattamento
Il legno massiccio o i materiali impiallacciati con specie pregiate vengono stampati di rado. Normalmente e tradizionalmente vengono verniciati o dipinti con vernici pigmentate. Le vernici hanno valore lucidante e decorativo, ma anche protettivo: servono a isolare il legno poroso da acqua e sporco. Quando si parla però di composti e derivati del legno, la stampa entra in ballo prepotentemente. Da decenni ormai è diffusa la pratica della “nobilitazione” di pannelli poco pregiati – solitamente truciolari, multistrato o pannelli di fibra di legno. Questa nobilitazione avviene attraverso l’incollaggio sulla superficie di carta stampata con tecnologia rotativa a imitazione del legno. La carta, trattata nella maggior parte dei casi con resina melamminica, viene applicata sotto pressione e a caldo, e diventa così parte integrante del pannello. Negli ultimi anni sta prendendo piede anche la stampa digitale, che viene fatta direttamente sul materiale. Solitamente si usano MDF o comunque pannelli che presentino una superficie abbastanza liscia e omogenea. La tecnologia più usata è quella UV e UV LED, che offre buone prestazioni in termini di resistenze e di qualità di stampa. Per migliorare la coerenza cromatica, la resa quantitativa dell’inchiostro e la qualità di stampa, le superfici legnose vengono pretrattate con sostanze a base polimerica, poliuretanica o acrilica. Questi liquidi di pretrattamento vengono spruzzati sulla superficie o stesi con rulli e passati in forni per asciugare, e costituiscono la vera e propria base per la stampa. Per produzioni industriali vengono usate macchine single pass, ma possono essere usate anche stampanti flatbed ad alta produttività con sistemi automatizzati di carico e scarico del materiale. I vantaggi della stampa digitale sono diversi: lavorando on-demand, possono essere praticamente annullati i costi di magazzino; si possono creare infiniti pattern e design a imitazione del legno; con alcune tecnologie si possono riprodurre le venature del legno a registro con la stampa.In tutti i casi, a seconda degli usi finali, possono essere aggiunti post trattamenti per aumentare le resistenze all’abrasione, al graffio, al calpestio, all’umidità. Possono essere vernici, spruzzate o stese con rulli sui pannelli, oppure addirittura lamine polimeriche, incollate e pressate ad alta temperatura.
Creare l’effetto legno
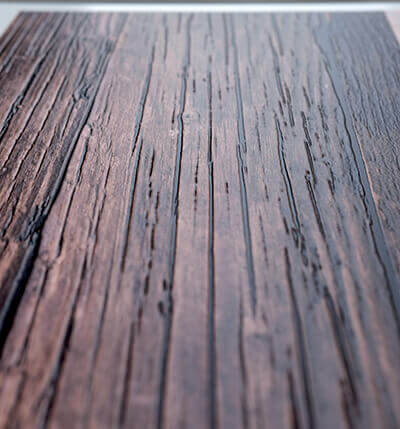
Un esempio di stampa digitale con effetto tattile a registro con l’immagine
Nell’industria dell’arredamento e dell’interior design, una delle sfide più grandi è creare un “effetto legno” convincente e verosimile. Oltre alla resa cromatica, complicata dal metamerismo, è di vitale importanza restituire l’effetto tattile del legno: tridimensionalità delle venature, temperatura, naturalità. Ci sono vari modi per ottenere risultati di livello da medio a ottimo – anche a seconda della qualità e delle resistenze richieste per il prodotto finito, dei costi, dei volumi produttivi. Nell’ambito della stampa tradizionale, i rotoli di carta melamminica vengono stampati con combinazioni di tinte spot che vanno dal beige al marrone scuro. In questo caso, l’effetto tridimensionale delle venature viene delegato a trattamenti analogici come presse a caldo, che imprimono la texture desiderata. Solitamente il prodotto che deriva da questo processo è di qualità media, e le venature non sono a registro con la stampa. Passando al digitale, alcune tecnologie prevedono l’uso della quadricromia tipica del mercato delle arti grafiche, magari con l’aggiunta di alcuni colori speciali. Altre, per ridurre il rischio di metamerismo, mutuano l’uso di combinazioni di tinte marroni da altri settori, come la stampa digitale su ceramica e vetro. Per quanto riguarda la riproduzione delle venature, alcune delle più avanzate tecnologie digitali riescono a riprodurre la texture del legno perfettamente a registro con la stampa. Questo può avvenire sia con tecnologia additiva, sia con tecnologia chimico-sottrattiva. La prima prevede l’aggiunta di strati di materiale per creare lo spessore, passaggio dopo passaggio, mentre la seconda prevede l’uso di speciali sostanze chimiche che, grazie alla loro “incompatibilità” con il coating su cui agiscono, fanno si che questo si ritragga nei punti desiderati, creando le scanalature.
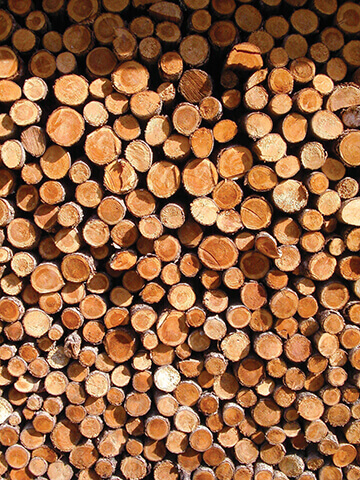
Tronchi pronti alla lavorazione
Anisotropia: proprietà di un materiale che ha caratteristiche diverse a seconda della direzione lungo la quale vengono considerate. Il legno è un materiale anisotropo: le sue variazioni dimensionali variano a seconda della direzione delle fibre.
Dicotiledoni: classe delle angiosperme che comprende piante sia erbacee che legnose.
Durabilità: proprietà di un materiale di conservare le caratteristiche fisiche e meccaniche durante un periodo di tempo, sotto l’azione di diversi agenti.
Igroscopicità: capacità di un materiale di assorbire l’umidità presente in aria. Le sostanze igroscopiche cambiano aspetto, colore o dimensione, per cui possono rivelare lo stato di umidità dell’aria.
Impiallacciatura: copertura di un supporto ligneo non pregiato con un piallaccio di legno pregiato, che viene incollato sopra.
Massello: legno da lavorazione costituito da un pezzo unico, usato solitamente per parquet e mobili pregiati. Il massello non è impiallacciato né placcato. Attenzione: è un sostantivo, anche se spesso viene usato come sinonimo dell’aggettivo “massiccio”.
Metamerismo: fenomeno ottico per cui colori che sembrano uguali sotto una certa luce, si rivelano invece diversi se sono illuminati con una luce diversa.
Minuzzolo: letteralmente “pezzettino minuto, piccolissima parte di cosa sminuzzata”. Piccoli pezzi di legno fragile, di scarto, riciclato.
Porosità: il rapporto tra il volume dei vuoti (pori) e il volume totale del materiale considerato.
Proprietà tecnologica: definisce l’attitudine di un materiale a essere sottoposto a diverse lavorazioni. Per esempio, sono proprietà tecnologiche malleabilità, fusibilità, saldabilità, truciolabilità. Definiscono quindi la capacità del materiale di lasciarsi lavorare, rispettivamente, per deformazione plastica, fusione, unione di lembi e asportazione di truciolo con macchine utensili.