Il PVC è uno dei materiali polimerici più diffusi al mondo. Lo troviamo sotto forma di plastica estremamente rigida e dura, usato per esempio per i serramenti. Ma è famoso anche per essere uno dei materiali più morbidi ed elastici, e viene usato per esempio nel wrapping. Cosa gli permette di assumere proprietà così diverse? E come si può stampare?
Un paio di numeri fa, all’inizio del nostro viaggio alla scoperta dei materiali e della loro stampabilità, abbiamo cercato di capire meglio cos’è la plastica. Ovviamente, la prima cosa che abbiamo notato è che esistono moltissimi tipi diversi di plastica, dalle caratteristiche chimiche e fisiche anche completamente diverse tra loro. In questo numero approfondiremo una particolare tipologia di plastica, davvero molto diffusa e versatile: il PVC. Sono fatti di questo materiale mobili, pavimenti, infissi, parti di automobili, e perfino le carte di credito. Anche nel caso del PVC, quando parliamo di stampa ci dobbiamo fare alcune domande:
- Qual è la destinazione d’uso del prodotto finito?
- Che resistenze sono necessarie, durante la lavorazione e dopo?
- Quali lavorazioni sono necessarie per arrivare al prodotto finito?
- In che modo posso rendere la lavorazione e il prodotto finito sostenibili per l’ambiente e le persone?
Queste domande sono fondamentali per capire in che modo rispettare la normativa sulla sicurezza, tenendo presente che oltre a questa, chi lavora con il PVC si attiene spesso anche a un impegno volontario per lo sviluppo sostenibile dell’industria europea, detto VinylPlus. Rispondere a queste domande iniziali sarà propedeutico a queste:
- Ho bisogno di pretrattamento e post-trattamento?
- Quale tecnica di stampa userò?
- Quale inchiostro?
- Come verrà lavorato il prodotto dopo la stampa?
Duro, morbido, ma sempre PVC: un po’ di chimica
La sigla PVC sta per “polivinilcloruro”, nome che fa immediatamente intuire la sua composizione chimica. “Poli”, in greco, significa “molti”, ed è la stessa particella che ritroviamo nella parola “polimero”. “Vinil” fa subito pensare al vinile – che infatti è uno dei nomi con cui è noto il PVC – e “cloruro” richiama alla mente il cloro – che non a caso è uno dei suoi componenti. Il PVC è stato scoperto a metà dell’Ottocento. Si forma a partire da da due materiali facilmente ritrovabili in natura: sale (per il 57%) e petrolio (per il 43%). Dal primo si ottiene il cloro, attraverso l’elettrolisi dell’acqua salata, e dal secondo l’etilene. Combinati insieme, cloro gassoso ed etilene formano il 1,2-dicloroetano (dicloruro di etilene o 1,2-DCE), intermedio per la produzione del monomero di cloruro di vinile o vinilcloruro (CVM). Un altro modo per ottenere il 1,2-dicloroetano è dalla reazione di etilene e acido cloridrico. Il passaggio da monomero a polimero si chiama (appunto) polimerizzazione, e avviene attraverso l’unione di più monomeri di cloruro di vinile in modo che si formino lunghe molecole lineari. Questo processo dà origine alla resina, che si presenta sotto forma di polvere fine e bianca (tipo zucchero o sabbia sottile). È a questa resina che vengono aggiunti gli additivi più diversi, così da ottenere le caratteristiche che di volta in volta il PVC deve avere, a seconda della destinazione d’uso del prodotto finito: resistenza, durezza, elasticità… Gli additivi possono essere di vari tipi: stabilizzanti, per mantenere le caratteristiche chimico-fisiche del materiale, impedendone l’invecchiamento e la degradazione termica; plastificanti, per migliorare la plasticità o fluidità del materiale; lubrificanti, per abbassare la viscosità della massa polimerica e far “scivolare” il polimero fuso lungo le pareti metalliche durante la lavorazione; filler, per migliorare alcune proprietà del materiale (scorrevolezza, miscibilità, resistenza all’urto, brillantezza superficiale, caratteristiche antifiamma…) e ogni tanto ottimizzare i costi (nel caso per esempio del carbonato di calcio); pigmenti, per colorare il materiale. Dalla miscelazione di questi elementi si ottengono i cosiddetti “compound”, che significa letteralmente “composto”. Questi compound possono avere la forma di granuli o essere in “dry blend”, ovvero sotto forma di polvere secca. I granuli si ottengono miscelando PVC da sintesi e additivi in un estrusore bivite. Da qui esce una specie di “spaghetto” di PVC che viene tagliato (in gergo “pellettizzato”) con delle lame a distanza regolare, così da assumere la forma di granulo. Sotto forma di “dry blend”, invece, il PVC viene mescolato con ulteriori additivi, setacciato e imballato come polvere asciutta. La produzione di compound non è semplice, e anzi richiede competenze chimiche, tecniche e legali specifiche, per ottemperare alla severa legislazione che norma il settore sia dal punto di vista dell’igiene che della sicurezza.
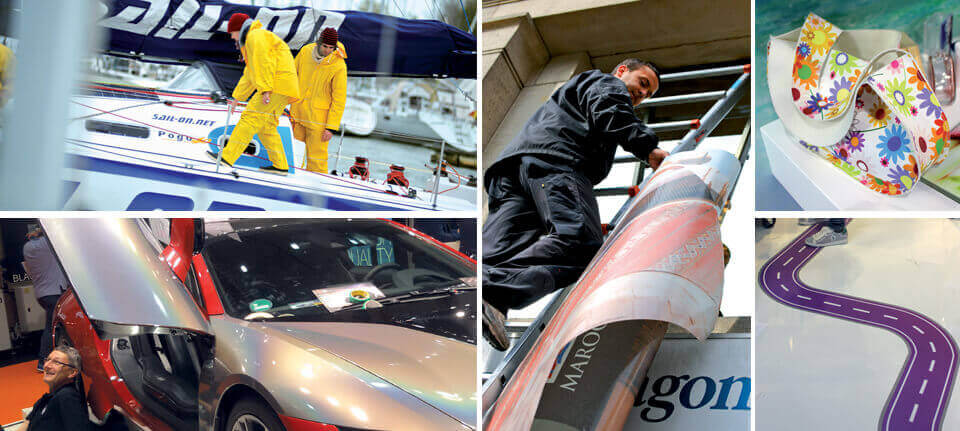
Il PVC è uno dei materiali polimerici più duttili. Viene usato nel mercato automotive e nautico, nel fashion, nella comunicazione visiva, nell’interior decoration. Foto: PVC Forum
Tutte le tecniche di lavorazione e di decorazione
A questo punto, il PVC sotto forma di compound o di dry blend è pronto per essere ulteriormente lavorato e assumere le caratteristiche necessarie per realizzare i prodotti finiti. Le lavorazioni alle quali può essere sottoposto variano enormemente proprio a seconda della destinazione d’uso e alla tipologia di decorazione richiesta. Grazie alla sua eccezionale versatilità, il PVC può assumere forme e caratteristiche estremamente diverse, ed è quasi incredibile pensare che gli infissi o il pavimento di casa (rigidi, opachi, estremamente duri e resistenti) siano fatti della stessa sostanza di cui è fatta la pellicola che usiamo per avvolgere gli alimenti (trasparente, elastica e sottilissima). Ottenere risultati così diversi è possibile perché si aggiungono additivi diversi, ma anche perché si parte da PVC qualitativamente diversi all’origine, con “valori K” anche molto diversi tra loro.
Lavorazione | Risultato | Applicazioni |
Calandratura: il materiale, mescolato in modo omogeneo con gli additivi, viene passato attraverso una serie di rulli riscaldati posizionati a distanza decrescente. | Film o fogli in PVC, di vario spessore e larghezza, che possono avere anche finiture superficiali particolari. | Fogli e lastre per la termoformatura per imballaggi e componenti sagomati, fogli rigidi e plastificati per l’industria cartotecnica e alimentare, carte plastificate (tipo carte di credito), tovaglie, abbigliamento, wallpaper e rivestimenti per l’interior decoration, film per il wrapping, tendaggi. |
Espansione: tecnica di lavorazione con la quale si varia il peso specifico del polimero di partenza per ottenere materiali più leggeri grazie all’uso di gas espandenti. | Espansi in PVC rigidi, semi rigidi, flessibili. | Materiali per l’isolamento termico e acustico, finte pelli, strutture alleggerite (tubi e profilati, battiscopa…). |
Estrusione: il materiale viene posizionato nella trafila o estrusore, dove una vite senza fine lo spinge verso l’esterno. Con l’aiuto del calore di attrito e del calore indotto esce dal foro d’uscita, detto filiera o matrice, che è sagomato secondo il profilo che deve avere il prodotto finito. Può essere abbinato al soffiaggio. | Tubi o film. | Tubi, profilati, film sottili, materiali continui, rivestimenti, cavi, fili. |
Estrusione + soffiaggio: un segmento di tubo estruso viene inserito nello stampo, dove viene insufflata aria al suo interno, così che assuma la forma desiderata. | Oggetti cavi a corpo unico. | Bottiglie, flaconi, contenitori. |
Iniezione + soffiaggio: il materiale semifluido viene iniettato attorno a un cannello di soffiaggio, dove viene insufflata aria così che aderisca alle pareti dello stampo e assuma la forma desiderata. | Oggetti cavi a corpo unico. | Bottiglie, flaconi, contenitori. |
Metallizzazione: i film calandrati in PVC vengono metallizzati per sublimazione di alluminio sotto vuoto. | Film metallizzato. | Regalistica e imballi per alimenti (caramelle, cioccolatini…). |
Rivestimento per immersione in letto fluido o in plastisol: l’oggetto da rivestire, preriscaldato, viene introdotto in un ambiente chiuso in cui la polvere di PVC, tenuta in sospensione, aderisce sulla superficie (letto fluido); viene poi inserito in un forno di cottura dove il rivestimento fonde e forma uno strato continuo. Analogamente, nell’immersione in plastisol lo stampo viene immerso in un plastisol semiliquido, che poi viene gelificato in forno e infine estratto dallo stampo, una volta raffreddato. | Oggetti di metallo o porcellana rivestiti. | Stivali, guanti, manopole… |
Rivestimento per spalmatura: un velo sottile di pasta di plastisol viene distribuito sul supporto tessile da rivestire con una “racla” (o spatola). Il nastro spalmato passa in forno, dove avviene la gelificazione dello strato di plastica, e infine attraverso cilindri di raffreddamento e di goffratura. |
Tessuti e “tessuti non tessuti” in resine sintetiche plastificati. | Tende, tovaglie, tessuti per arredamento e moda,finte pelli, supporti per la comunicazione visiva (banner). |
Stampaggio a iniezione: il materiale viene immesso in un cilindro riscaldato, dove fonde e viene spinto verso un foro di uscita con un pistone o una vite rotante e iniettato in uno stampo. Viene estratto una volta raffreddato e solidificato. | Oggetti o componenti anche molto complessi e precisi. | Componenti per automobili, arredamento, elettronica, industria, protesi artificiali. |
Stampaggio rotazionale: il dry blend o il plastisol viene introdotto in uno stampo cavo, posto in forno e fatto ruotare su due assi perpendicolari, così che la materia aderisca allo stampo grazie alla forza centrifuga; il pezzo viene poi raffreddato ed estratto. | Oggetti cavi a corpo unico. | Cruscotti per auto, articoli che in passato venivano realizzati per termoformatura, bambole, palloni. |
Termoformatura: le lastre termoplastiche rigide vengono posizionate sopra o sotto uno stampo che che può avere anche alveolature e cavità. Può essere realizzata sotto vuoto oppure sotto pressione; in entrambi i casi la lastra viene riscaldata (ma non fusa). |
Manufatti termoformati a seconda dello stampo. | Imballaggi, anche trasparenti, modellati in corrispondenza alla forma dell’oggetto da contenere, come per esempio i blister dei prodotti farmaceutici. |
La stampa e la verniciatura del PVC

La pellicola in PVC usata per gli alimenti può essere stampata con inchiostri appositi, come in questo esempio di Gruppo Fabbri. Foto: Gruppo Fabbri
Il PVC, una volta sottoposto a tutte queste trasformazioni, può essere ulteriormente lavorato. Per esempio, può essere stampato o verniciato. Essendo un materiale plastico, non è semplicissimo far aderire gli inchiostri, tradizionali o digitali che siano, e le vernici. Come abbiamo spiegato nell’articolo dedicato alla plastica, su WIDE 38, sono necessari pretrattamenti chimici (primer di vario tipo) e fisici (fiammatura, plasma atmosferico, trattamento corona). Non solo: bisogna sottoporre i prodotti a un ottimo curing per asciugare perfettamente gli inchiostri, e talvolta sottoporli anche a post-trattamenti per fissarli meglio. In determinati settori che hanno bisogno di resistenze molto alte, come nel caso dei pavimenti in PVC, le stampe devono essere protette addirittura con delle laminazioni. Le difficoltà di stampa del PVC sono dovute alla tensione superficiale dei polimeri, che rendono ardua l’adesione e la bagnabilità. Normalmente, su PVC si stampa con inchiostri UV, UV LED, ecosolvent, ma anche gli inchiostri a base acqua offrono delle ottime performance in alcuni settori. Si può stampare in digitale, in serigrafia, in tampografia e flessografia. Si trovano in commercio anche inchiostri speciali a bassa migrazione, adatti per applicazioni nel settore food. Anche in questo caso, è fondamentale capire quali resistenze dovrà avere il prodotto finito: un conto sono gli infissi decorati con effetto legno, e un altro sono le pellicole per avvolgere gli alimenti. C’è un ulteriore aspetto da tenere in considerazione: sulla base dell’inchiostro o della vernice scelti si può avere la possibilità di nobilitare o meno il prodotto finito con hot foil. Di solito si sceglie di tenere in macchina inchiostri sovrastampabili, per motivi pratici. Nel caso in cui siano necessarie resistenze chimiche o meccaniche superiori, si può passare a quelli non sovrastampabili.
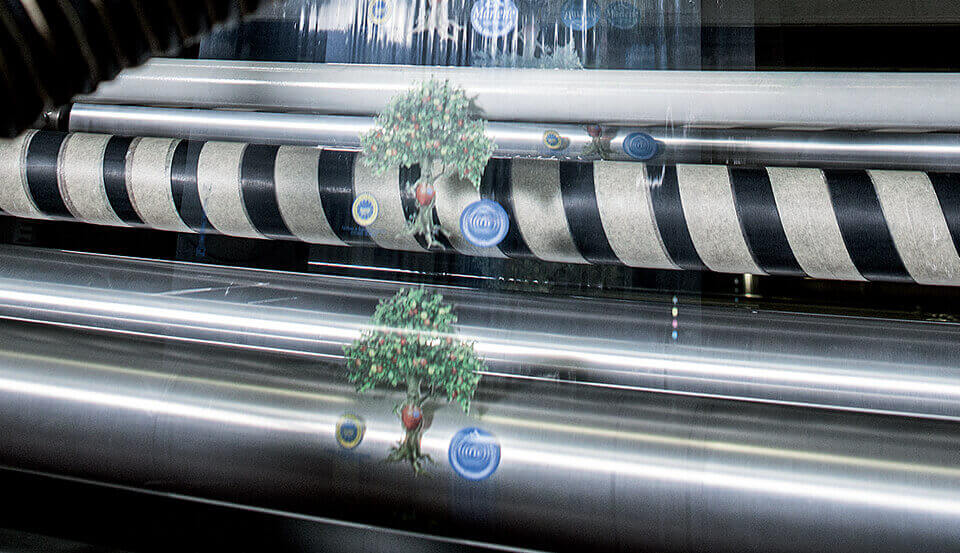
Film alimentare in PVC stampato nella sede del Gruppo Fabbri, a Vignola in provincia di Modena.
PVC e ambiente: produzione sostenibile e riciclo
Due delle grandi innovazioni ambientali legate al PVC sono la possibilità di rendere la produzione sempre più sostenibile e di potenziare il riciclo. Queste preoccupazioni sono condivise dalle aziende che fanno parte della filiera, impegnate anche a livello volontario nella risoluzione di questi problemi. I produttori europei di PVC, riuniti nell’associazione ECVM (European Council of Vinyl Manufacturers), hanno deciso di applicare un proprio protocollo, l’ECVM Charter, a cui tutti devono far riferimento per ridurre l’impatto ambientale della produzione. Ma è VinylPlus il più importante programma di Impegno Volontario per la sostenibilità dell’industria europea del PVC, che prevede il coinvolgimento di tutta la filiera per rendere la produzione sempre più ecologica e gestire il problema del fine vita dei prodotti. Per quanto riguarda il primo punto, le moderne metodologie e tecnologie di produzione del PVC sono state studiate e migliorate per minimizzare l’impatto sull’ambiente e i rischi per la salute dei lavoratori e della popolazione che abita vicino agli stabilimenti. Per esempio, le celle a mercurio e a diaframma usate per il processo di elettrolisi del cloruro di sodio sono state sostituite da celle a membrana, più sicure ed ecologiche. Gli impianti di produzione usano sistemi di produzione automatizzati, a ciclo chiuso e integrato, che permettono da un lato di controllare e recuperare i sottoprodotti, e dall’altro di abbattere le emissioni inquinanti. Per quanto riguarda invece il secondo punto, l’ultimo bilancio di VinylPlus, che risale al 2017, conferma un trend del riciclo in costante crescita. Nel 2017 sono state riciclate 639.648 tonnellate di PVC, +12% rispetto al 2016, e in linea con l’obiettivo di recuperarne 800.000 all’anno entro il 2020. Oltre 300 mila tonnellate provengono da profili finestra, tapparelle, scuri e altri profili per edilizia. Dal 2000 a oggi VinylPlus ha recuperato e riciclato oltre quattro milioni di tonnellate di PVC; nel 2017 le prime due nazioni europee per quantità di PVC riciclato sono state la Germania e l’Inghilterra, seguite da Italia e Francia. Il PVC recuperato viene di solito “tagliato” con percentuali variabili di polimero vergine. Il PVC rigido riciclato viene usato soprattutto per produrre tubi, profilati, barriere antirumore e monofili per spazzole. Quello plastificato, che costituisce una buona parte del PVC riciclato, viene usato principalmente per realizzare tubi da giardino, membrane impermeabilizzanti, separatori per il traffico, tappetini e paraspruzzi per il settore automotive e suole per l’industria calzaturiera.
Compound: una delle forme intermedie del PVC ottenuta mescolando la resina con diversi additivi (stabilizzanti, plastificanti, lubrificanti, filler e pigmenti). Possono essere in granuli o dry blend, cioè come polvere. I granuli vengono ottenuti tramite estrusione e il dry blend attraverso la semplice miscelazione dei componenti.
Dry blend: una delle due forme che possono assumere i compound di PVC. Letteralmente significa “miscela asciutta”.
Estrusione: processo di lavorazione del PVC che permette di ottenere i compound, granuli di sezione identica tagliati da “spaghetti” di materiale tagliati a intervalli regolari.
Intermedio: un materiale derivante dalle materie prime, ma che non ha ancora assunto la forma definitiva. Nella produzione del PVC, intermedi si possono considerare i compound.
Plastificante: sostanza che viene aggiunta per rendere un materiale più morbido ed elastico. Nel caso del PVC flessibile, vengono generalmente usati ftalati, plastificanti polimerici e plastificanti trimellitati.
Plastisol: sospensione di particelle di PVC in un fluido plastificante.
Polimerizzazione: reazione chimica che porta alla formazione di una catena polimerica, dai monomeri di partenza. Nel caso del PVC avviene solitamente in sospensione o in emulsione, e talvolta in massa.
PVC-C: PVC post clorurato, presenta caratteristiche di maggiore resistenza agli agenti ossidativi e all’alta temperatura.
PVC-O o PVC orientato: mescola in PVC che dopo la lavorazione subisce un processo di orientazione molecolare che le conferisce caratteristiche fisico-meccaniche uniche: aumento dell’elasticità, migliore resistenza agli urti, minore capacità di propagazione delle cricche (le fratture), maggior resistenza ai colpi d’ariete (l’urto di un fluido in movimento che impatta contro una parete).
PVC-P: è il PVC flessibile, la sigla significa “polivinilcloruro con plastificante”, usato nella produzione di articoli flessibili.
PVC-U: PVC rigido, che non impiega plastificanti, usato nella produzione di profili finestre e tubi rigidi.
Valore K: caratteristica della resina PVC che indica la lunghezza delle molecole del polimero di cui è composto. Questo valore, solitamente, è compreso tra 35 e 80. Una resina di PVC di valore K basso è facilmente lavorabile ma ha una bassa qualità, mentre una resina di valore K alto implica una difficoltà di lavorazione, ma ha ottime qualità. In ambito industriale, solitamente vengono usate resine con valore K compreso tra 60 e 70.